واحدهاي عملیاتی
واحدهاي عملیاتی
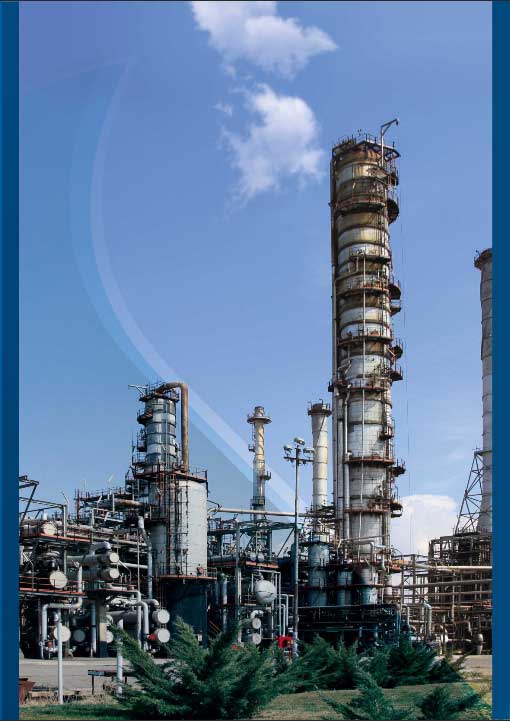
این واحد از دو قسمت تقطیر در فشار جو و تقطیر در خلاء تشكیل یافته است. در این واحد نفت خام بصورت برشهای متفاوت از هم جدا می شود.
نخستین مرحله پالایش نفت خام،تقطیر در فشار جو است که برشهای اصلی نفت خام را از یکدیگر جدا میكند. برای این منظور نفت خام پس از عبور از مبدلهای حرارتی "پیش گرمایش" و کوره تا حدود 350 درجه سانتی گراد گرم شده،سپس به برج تقطیر درجو وارد میشود. فرآورده های برج تقطیر در فشار جو عبارتند از:
- محصولات بالای برج شامل: گازهای سبك، گاز مایع، نفتای سبك و سنگین
- محصولات جانبی برج شامل: نفتای امتزاج، حلال AW402 ، نفت سفید، نفت گاز سبك
- محصولات ته مانده برج ، خوراک واحد تقطیر در خلاء محسوب می شود
از این محصولات نفت سفید و حلال AW402 مطابق مشخصات لازم بعنوان فرآورده های نهایی به مخازن مربوطه انتقال می یابد. از میان محصولات بالای برج كه در برجهای دیگر تفكیك می شوند ، نفتای سنگین برای ارتقاء درجه آرام سوزی به واحد بنزین سازی انتقال یافته و محصول بدست آمده از این مرحله با نفتای سبك واحد تقطیر مخلوط می شود تا محصول نهائی بنزین مطابق استاندارد شركت ملی پالایش و پخش فرآورده های نفتی ایران تهیه شود . ظرفیت طراحی شده این واحد 80 هزار بشكه در روز بوده كه با اجرای طرح افزایش ظرفیت به 110 هزار بشكه در روز ارتقاء یافته است.
ته مانده برج تقطیر در فشار جو بعد از افزایش دما تا حدود 390 درجه سانتیگراد به برج تقطیر درخلاء ارسال می گردد در این برج به علت وجود خلاء نسبی ، مواد سنگین زودتر به نقطه جوش رسیده و عمل تفكیك آسان تر انجام می گیرد. محصولاتی كه در این مرحله به دست می آیند عبارتند از : نفت گاز سنگین ،خوراك واحد آیزوماكس (Isofeed) ،برش روغنی1 (LD1) ، برش روغنی2 (LD2) ، سلاپس واكسی (Slopwax) و ته مانده برج تقطیر در خلاء . از اختلاط نفت گاز سنگین با نفت گاز سبك واحد تقطیر در فشار جو محصول نهائی نفت گاز (گازوئیل) تهیه می شود. Isofeed جهت تبدیل به مواد سبك تر به واحد آیزوماكس (هیدروكراكر) ارسال می گردد. بخشی از محصول ته مانده برج تقطیر در خلاء به عنوان خوراك واحد قیر سازی و بخشی از آن جهت تولید نفت كوره و تبدیل به مواد سبك تر به واحد كاهش گرانروی انتقال و مقداری از آن به شركتهای خصوصی تولید كننده قیر واگذار می گردد. همچنین LD1و LD2 به عنوان مواد اولیه تولید روغنهای صنعتی به شركتهای متقاضی ارسال می شود. ظرفیت طراحی این واحد معادل 37440 بشكه در روز بوده كه با انجام تغییراتی طی پروژه CROS این میزان تا 50400 بشكه در روز افزایش یافته است.
این واحد از دو قسمت تقطیر در فشار جو و تقطیر در خلاء تشكیل یافته است. در این واحد نفت خام بصورت برشهای متفاوت از هم جدا می شود.
نخستین مرحله پالایش نفت خام،تقطیر در فشار جو است که برشهای اصلی نفت خام را از یکدیگر جدا میكند. برای این منظور نفت خام پس از عبور از مبدلهای حرارتی "پیش گرمایش" و کوره تا حدود 350 درجه سانتی گراد گرم شده،سپس به برج تقطیر درجو وارد میشود. فرآورده های برج تقطیر در فشار جو عبارتند از:
- محصولات بالای برج شامل: گازهای سبك، گاز مایع، نفتای سبك و سنگین
- محصولات جانبی برج شامل: نفتای امتزاج، حلال AW402 ، نفت سفید، نفت گاز سبك
- محصولات ته مانده برج ، خوراک واحد تقطیر در خلاء محسوب می شود
از این محصولات نفت سفید و حلال AW402 مطابق مشخصات لازم بعنوان فرآورده های نهایی به مخازن مربوطه انتقال می یابد. از میان محصولات بالای برج كه در برجهای دیگر تفكیك می شوند ، نفتای سنگین برای ارتقاء درجه آرام سوزی به واحد بنزین سازی انتقال یافته و محصول بدست آمده از این مرحله با نفتای سبك واحد تقطیر مخلوط می شود تا محصول نهائی بنزین مطابق استاندارد شركت ملی پالایش و پخش فرآورده های نفتی ایران تهیه شود . ظرفیت طراحی شده این واحد 80 هزار بشكه در روز بوده كه با اجرای طرح افزایش ظرفیت به 110 هزار بشكه در روز ارتقاء یافته است.
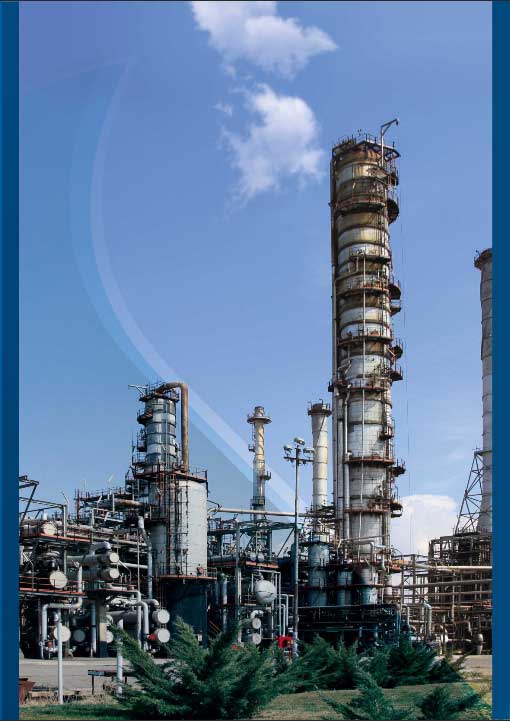
ته مانده برج تقطیر در فشار جو بعد از افزایش دما تا حدود 390 درجه سانتیگراد به برج تقطیر درخلاء ارسال می گردد در این برج به علت وجود خلاء نسبی ، مواد سنگین زودتر به نقطه جوش رسیده و عمل تفكیك آسان تر انجام می گیرد. محصولاتی كه در این مرحله به دست می آیند عبارتند از : نفت گاز سنگین ،خوراك واحد آیزوماكس (Isofeed) ،برش روغنی1 (LD1) ، برش روغنی2 (LD2) ، سلاپس واكسی (Slopwax) و ته مانده برج تقطیر در خلاء . از اختلاط نفت گاز سنگین با نفت گاز سبك واحد تقطیر در فشار جو محصول نهائی نفت گاز (گازوئیل) تهیه می شود. Isofeed جهت تبدیل به مواد سبك تر به واحد آیزوماكس (هیدروكراكر) ارسال می گردد. بخشی از محصول ته مانده برج تقطیر در خلاء به عنوان خوراك واحد قیر سازی و بخشی از آن جهت تولید نفت كوره و تبدیل به مواد سبك تر به واحد كاهش گرانروی انتقال و مقداری از آن به شركتهای خصوصی تولید كننده قیر واگذار می گردد. همچنین LD1و LD2 به عنوان مواد اولیه تولید روغنهای صنعتی به شركتهای متقاضی ارسال می شود. ظرفیت طراحی این واحد معادل 37440 بشكه در روز بوده كه با انجام تغییراتی طی پروژه CROS این میزان تا 50400 بشكه در روز افزایش یافته است.
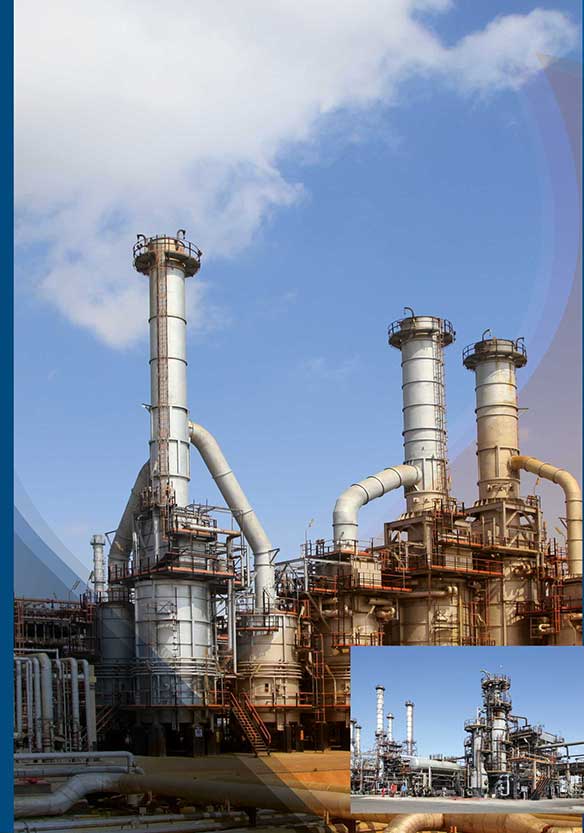
وظیفه این واحد كاهش ویسكوزیته محصول ته مانده برج تقطیر در خلاء ، بمنظور تولید فرآورده نفت كوره می باشد. ته مانده سنگینی که از پائین برج تقطیر در خلاء بدست می آید ، دارای گرانروی )ویسکوزیته) خیلی بالایی است كه قابل عرضه مستقیم به عنوان سوخت نفت کوره به بازار نیست .به همین دلیل ته مانده برج تقطیر در خلاء (و بعضاً مقداری از مواد Slopwax) به واحد کاهش گرانروی ارسال و در کوره واحد گرم میشود تامولکولهای سنگین در اثر حرارت شکسته شده و به مواد سبک تر و گاز تبدیل شود. محصول اصلی این واحد ، نفت کوره با گرانروی کمتر و محصولات فرعی نفت گاز سنگین ، بنزین نامرغوب (گوگرددار) و مقادیری گازهای سبك است. طی پروژه CROS ، بمنظور افزایش راندمان كاركرد فرآیند در این واحد راكتور Soaker نصب گردیده است . در صورت نیاز ، نفت كوره حاصل از این واحد جهت تصحیح برخی خصوصیات از جمله ویسكوزیته با مقداری نفت سفید ، نفت گاز ، Isofeed ، LD1 و LD2 مخلوط می شود. بنزین نامرغوب حاصل جهت تصفیه به واحد بنزین سازی انتقال می یابد. ظرفیت طراحی شده واحد كاهش گرانروی 16500 بشكه در روز است.
نفت گاز یا گازوئیلی كه از واحد تقطیر در فشار جو بدست می آید دارای مواد گوگردی بوده كه بعد از سوختن در موتورهای دیزل با تولید گازهای گوگردی سبب آلودگی محیط زیست می شود. در این واحد مواد گوگردی نفت گاز در راكتور با گاز هیدروژن تحت فشار و درجه حرارت معین و در حضور كاتالیست به سولفید هیدروژن تبدیل شده و طی فرآیندی از نفت گاز جدا می شود. هیدروژن مورد نیاز این واحد از واحد هیدروژن سازی و یا از واحد بنزین سازی قابل تامین است. ظرفیت طراحی این واحد 13500 بشكه در روز است.
وظیفه این واحد افزایش درجه آرام سوزی (عدد اكتان) بنزین خام بمنظور تولید بنزین موتور می باشد . نفتای حاصل از واحد تقطیر که دارای مواد گوگردی بالا و درجه آرام سوزی پایین است، ابتدا در دستگاه گوگردزدائی نفتا توسط گاز هیدروژن در مجاورت کاتالیزور)کبالت،مولبیدن و (...تصفیه شده و مواد گوگردی آن به صورت گاز سولفید هیدروژن جدا می شود . سپس نفتای تصفیه شده از دستگاه گوگردزدائی از نفتا با گازهای دارای هیدروژن بالا (بیش از 70 درصد هیدروژن ) حاصله از واحد تبدیل کاتالیستی مخلوط شده و تحت دما و فشار معین در چهار راکتور در مجاورت کاتالیزور پلاتین ، بر اثر فعل و انفعالات شیمیائی تغییرماهیت داده به ترکیباتی با درجه آرام سوزی بالا تبدیل می شود. بنزین حاصل از این دستگاه با نفتای سبك به دست آمده از واحد تقطیر ، در واحد مخازن به نسبت مشخصی مخلوط شده و پس از افزودن رنگ محصول بنزین نهائی تهیه می گردد. با ماهیت فعل و انفعالات انجام یافته در راكتورهای این واحد، مقداری گاز هیدروژن ، گاز سبك و گاز مایع نیز تولید می شوند. واحد گوگردزدائی از نفتا مصرف كننده گاز هیدروژن و واحد افزاینده درجه آرام سوزی به عنوان تولید كننده هیدروژن محسوب می شوند، بنابر این مازاد هیدروژن دستگاه تبدیل كاتالیستی به عنوان خوراك واحد هیدروژن به آن واحد انتقال می یابد. ظرفیت طراحی شده دستگاه گوگردزدائی از نفتا9700 بشكه در روز و دستگاه تبدیل كاتالیستی 11000 بشكه در روز است.
وظیفه این واحد كاهش ویسكوزیته محصول ته مانده برج تقطیر در خلاء ، بمنظور تولید فرآورده نفت كوره می باشد. ته مانده سنگینی که از پائین برج تقطیر در خلاء بدست می آید ، دارای گرانروی )ویسکوزیته) خیلی بالایی است كه قابل عرضه مستقیم به عنوان سوخت نفت کوره به بازار نیست .به همین دلیل ته مانده برج تقطیر در خلاء (و بعضاً مقداری از مواد Slopwax) به واحد کاهش گرانروی ارسال و در کوره واحد گرم میشود تامولکولهای سنگین در اثر حرارت شکسته شده و به مواد سبک تر و گاز تبدیل شود. محصول اصلی این واحد ، نفت کوره با گرانروی کمتر و محصولات فرعی نفت گاز سنگین ، بنزین نامرغوب (گوگرددار) و مقادیری گازهای سبك است. طی پروژه CROS ، بمنظور افزایش راندمان كاركرد فرآیند در این واحد راكتور Soaker نصب گردیده است . در صورت نیاز ، نفت كوره حاصل از این واحد جهت تصحیح برخی خصوصیات از جمله ویسكوزیته با مقداری نفت سفید ، نفت گاز ، Isofeed ، LD1 و LD2 مخلوط می شود. بنزین نامرغوب حاصل جهت تصفیه به واحد بنزین سازی انتقال می یابد. ظرفیت طراحی شده واحد كاهش گرانروی 16500 بشكه در روز است.
نفت گاز یا گازوئیلی كه از واحد تقطیر در فشار جو بدست می آید دارای مواد گوگردی بوده كه بعد از سوختن در موتورهای دیزل با تولید گازهای گوگردی سبب آلودگی محیط زیست می شود. در این واحد مواد گوگردی نفت گاز در راكتور با گاز هیدروژن تحت فشار و درجه حرارت معین و در حضور كاتالیست به سولفید هیدروژن تبدیل شده و طی فرآیندی از نفت گاز جدا می شود. هیدروژن مورد نیاز این واحد از واحد هیدروژن سازی و یا از واحد بنزین سازی قابل تامین است. ظرفیت طراحی این واحد 13500 بشكه در روز است.
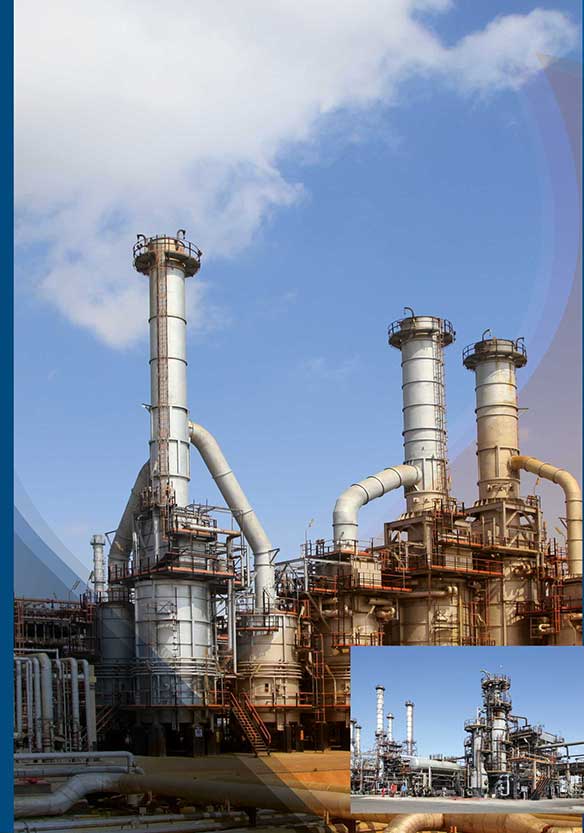
وظیفه این واحد افزایش درجه آرام سوزی (عدد اكتان) بنزین خام بمنظور تولید بنزین موتور می باشد . نفتای حاصل از واحد تقطیر که دارای مواد گوگردی بالا و درجه آرام سوزی پایین است، ابتدا در دستگاه گوگردزدائی نفتا توسط گاز هیدروژن در مجاورت کاتالیزور)کبالت،مولبیدن و (...تصفیه شده و مواد گوگردی آن به صورت گاز سولفید هیدروژن جدا می شود . سپس نفتای تصفیه شده از دستگاه گوگردزدائی از نفتا با گازهای دارای هیدروژن بالا (بیش از 70 درصد هیدروژن ) حاصله از واحد تبدیل کاتالیستی مخلوط شده و تحت دما و فشار معین در چهار راکتور در مجاورت کاتالیزور پلاتین ، بر اثر فعل و انفعالات شیمیائی تغییرماهیت داده به ترکیباتی با درجه آرام سوزی بالا تبدیل می شود. بنزین حاصل از این دستگاه با نفتای سبك به دست آمده از واحد تقطیر ، در واحد مخازن به نسبت مشخصی مخلوط شده و پس از افزودن رنگ محصول بنزین نهائی تهیه می گردد. با ماهیت فعل و انفعالات انجام یافته در راكتورهای این واحد، مقداری گاز هیدروژن ، گاز سبك و گاز مایع نیز تولید می شوند. واحد گوگردزدائی از نفتا مصرف كننده گاز هیدروژن و واحد افزاینده درجه آرام سوزی به عنوان تولید كننده هیدروژن محسوب می شوند، بنابر این مازاد هیدروژن دستگاه تبدیل كاتالیستی به عنوان خوراك واحد هیدروژن به آن واحد انتقال می یابد. ظرفیت طراحی شده دستگاه گوگردزدائی از نفتا9700 بشكه در روز و دستگاه تبدیل كاتالیستی 11000 بشكه در روز است.
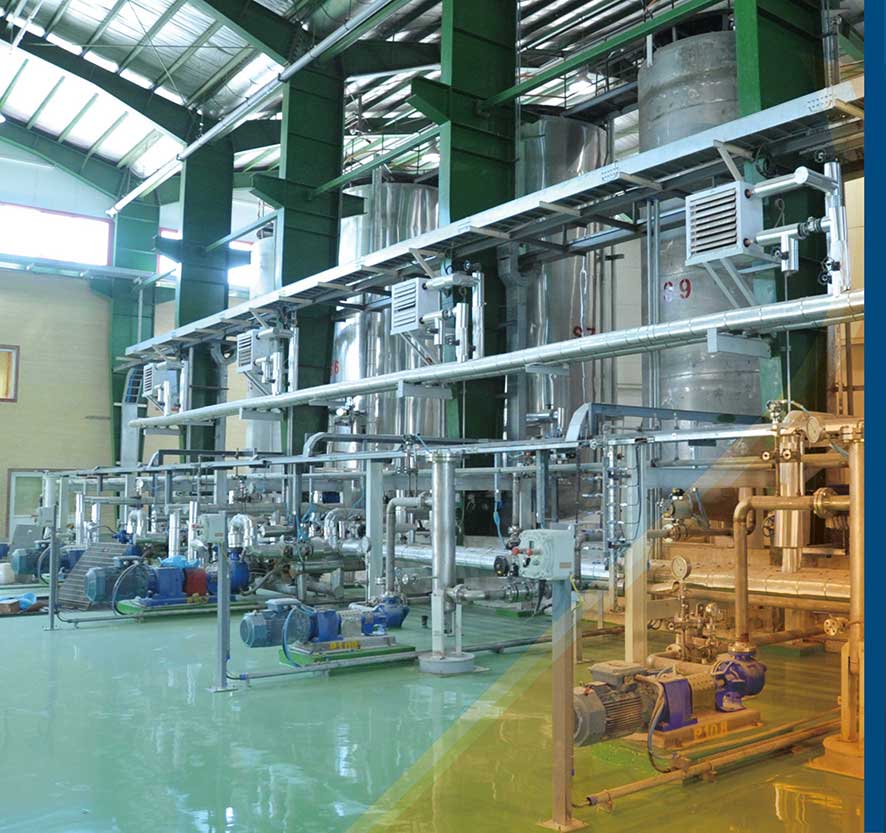
با پیشرفت صنعت و استفاده از تجهیزات و ماشین های مدرن، استفاده از روغن های با كیفیت بالا اهمیت زیادی پیدا كرده است. واحد اختلاط و تولید روغن های روانساز شركت پالایش نفت تبریز با استفاده از تكنولوژی و تجهیزات روز دنیا و با ظرفیت 40 هزار تن در سال با هدف تولید انواع روغن های موتور بنزینی ، دیزلی، صنعتی، دریایی و 10هزار تن در سال ضد یخ تأسیس شده است. در این واحد برای تولید روغن با توجه به فرمولاسیون و لایسنس مربوطه اكثرا از روغن های پایه (Base Oil ) مرغوب گروه های دو و سه استفاده می گردد كه با افزودن مواد افزودنی ( Additives ) شركت های معتبر اروپایی جهت بهبود خواص روانكاری، محصولات مختلف تولید می شود .
این واحد به منظور كاهش میزان گوگرد موجود در نفت گاز مطابق استاندارد یورو پنج (Euro V ) به زیر 10ppm طراحی گردیده است. خوراك واحد فوق مخلوط گازوئیل به میزان 30000 بشكه در روز می باشد. در این واحد گازوئیل در دو راكتور متوالی تحت فشار بالای گاز هیدروژن و حضور كاتالیست، تصفیه هیدروژنی شده و گوگرد و نیتروژن آن بترتیب بصورت گاز سولفید هیدروژن و آمونیاك جدا می گردد. گاز سولفید هیدروژن تولیدی در این فرآیند برای تبدیل به گوگرد به واحد گوگردسازی و گازوئیل تصفیه شده به واحد مخازن و نفتای تولیدی در طی فرآیند به واحد تقطیر ارسال می گردد . لازم به ذكر است واحد فوق مجهز به فرآیند شیرین سازی گاز با آمین می باشد. طراحی و ساخت واحد تصفیه هیدروژنی گازوئیل جدید علی رغم وجود واحد تصفیه هیدروژنی گازوئیل قدیم در راستای سیاست های شركت جهت عرضه سوخت پاك و مطابق استاندارهای زیست محیطی می باشد .
با پیشرفت صنعت و استفاده از تجهیزات و ماشین های مدرن، استفاده از روغن های با كیفیت بالا اهمیت زیادی پیدا كرده است. واحد اختلاط و تولید روغن های روانساز شركت پالایش نفت تبریز با استفاده از تكنولوژی و تجهیزات روز دنیا و با ظرفیت 40 هزار تن در سال با هدف تولید انواع روغن های موتور بنزینی ، دیزلی، صنعتی، دریایی و 10هزار تن در سال ضد یخ تأسیس شده است. در این واحد برای تولید روغن با توجه به فرمولاسیون و لایسنس مربوطه اكثرا از روغن های پایه (Base Oil ) مرغوب گروه های دو و سه استفاده می گردد كه با افزودن مواد افزودنی ( Additives ) شركت های معتبر اروپایی جهت بهبود خواص روانكاری، محصولات مختلف تولید می شود .
این واحد به منظور كاهش میزان گوگرد موجود در نفت گاز مطابق استاندارد یورو پنج (Euro V ) به زیر 10ppm طراحی گردیده است. خوراك واحد فوق مخلوط گازوئیل به میزان 30000 بشكه در روز می باشد. در این واحد گازوئیل در دو راكتور متوالی تحت فشار بالای گاز هیدروژن و حضور كاتالیست، تصفیه هیدروژنی شده و گوگرد و نیتروژن آن بترتیب بصورت گاز سولفید هیدروژن و آمونیاك جدا می گردد. گاز سولفید هیدروژن تولیدی در این فرآیند برای تبدیل به گوگرد به واحد گوگردسازی و گازوئیل تصفیه شده به واحد مخازن و نفتای تولیدی در طی فرآیند به واحد تقطیر ارسال می گردد . لازم به ذكر است واحد فوق مجهز به فرآیند شیرین سازی گاز با آمین می باشد. طراحی و ساخت واحد تصفیه هیدروژنی گازوئیل جدید علی رغم وجود واحد تصفیه هیدروژنی گازوئیل قدیم در راستای سیاست های شركت جهت عرضه سوخت پاك و مطابق استاندارهای زیست محیطی می باشد .
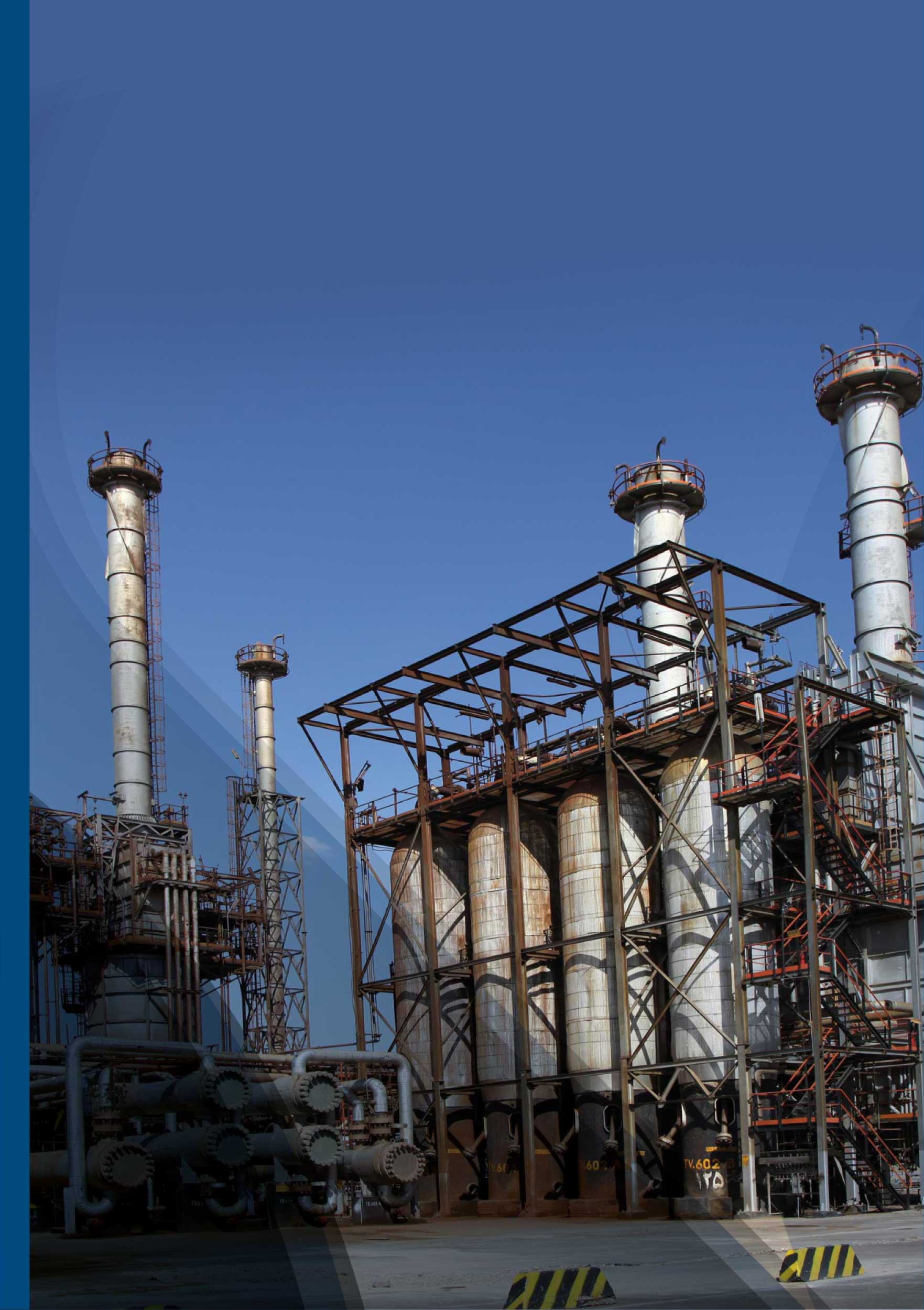
وظیفه این واحد تأمین هیدروژن واحد آیزوماكس و سایر واحدهای مصرف كننده هیدروژن در صورت نیاز میباشد . خوراك واحد هیدروژن گازهای سبك مانند متان، اتان و پروپان است كه عمدتاً از طریق گازهای غنی از هیدروژن واحد های بنزین سازی ، گازهای بخش فشار بالای تصفیه گاز با آمین و گاز طبیعی تامین می شود. خوراك این واحد پس از گوگرد زدایی و کلر زدایی تحت شرایط معین با بخارآب مخلوط شده و سپس به كوره "ریفرمر" هدایت میشود . دراین كوره گازهای هیدروكربوری با بخار آب در مجاورت كاتالیزور نیكل واكنش داده و به هیدروژن ، منواكسید كربن و دی اكسید كربن تبدیل میشود . در مراحل بعد در مجاورت كاتالیزور دیگــری تقریباً تمام حجـم گاز منواكسید كربن به گاز دی اكسید كربن تبدیل شده و سپس از جریان گاز هیــدروژن ، دی اكسید كربن در برج جذب در تماس با محلول آمین حذف می گردد. بدین ترتیب هیدروژن با درجه خلوص 94 درصد تهیه و به واحدهای مصرف كننده منتقل می شود . ظرفیت طراحی این واحد 34 میلیون فوت مكعب گاز هیدروژن در روز میباشد. لازم بذكر است با توجه به تولید هیدروژن با خلوص بالا در واحد بنزین سازی جدید امكان از سرویس خارج كردن واحد هیدروژن سازی مقدور می باشد.
وظیفه واحد آیزوماکس تبدیل برش آیزوفید (Isofeed) به فرآورده های مفیدی نظیر نفتا ، نفت سفید و نفت گاز سبک است. آیزوفید (Isofeed) حاصل از تقطیر در خلاء،پس از خروج از این برج خوراك واحد را تشکیل می دهد. در این واحد خوراك ابتدا با "گاز هیدروژن" مخلوط و پس از گرم شدن در كوره تحت درجه حرارت معین و فشار زیاد وارد راكتور می شود و در مجاورت كاتالیزور (نیكل ، مولیبدن و... ) مولكولهای سنگین شكسته شده و مواد نیتروژنی وگوگردی آن با هیدروژن ترکیب و به گاز آمونیاک و سولفید هیدروژن تبدیل میشود. محصولات این فعل و انفعالات پس از خروج از راکتورها به قسمت تفکیک ارسال می گردند. در برج های این قسمت گازهای سبك ، بوتان ، نفتای سبک و سنگین، نفت سفید و نفت گاز از یکدیگرجدا می شوند . نفتای سنگین حاصل، جهت اصلاح درجه آرام سوزی به واحدهای بنزین سازی و یا مخازن ارسال و نفتای سبك برای اختلاط با محصول نهائی بنزین استفاده می شود. نفت سفید و نفت گاز واحد آیزوماكس بسیار مرغوب است و پس از اختلاط با نفت سفید و نفت گاز واحد تقطیر به صورت محصولات نهائی عرضه می شود. خاطر نشان می گردد نفت سفید واحد آیزوماكس در تهیه سوخت هواپیما (ATK) مورد استفاده قرار می گیرد. بخشی از خوراك كه به مواد سبكتر شكسته نشده اند با آیزوفید مخلوط و مجدداً تحت واكنش هیدروكراكینگ قرار می گیرند و مازاد آن به عنوان محصول آیزوریسایكل قابل عرضه می باشد. هیدروژن مورد نیاز این واحد از طریق واحد هیدروژن سازی یا واحد بنزین سازی جدید تامین می شود. ظرفیت طراحی واحد آیزوماكس 18 هزار بشكه در روز است.
وظیفه این واحد تأمین هیدروژن واحد آیزوماكس و سایر واحدهای مصرف كننده هیدروژن در صورت نیاز میباشد . خوراك واحد هیدروژن گازهای سبك مانند متان، اتان و پروپان است كه عمدتاً از طریق گازهای غنی از هیدروژن واحد های بنزین سازی ، گازهای بخش فشار بالای تصفیه گاز با آمین و گاز طبیعی تامین می شود. خوراك این واحد پس از گوگرد زدایی و کلر زدایی تحت شرایط معین با بخارآب مخلوط شده و سپس به كوره "ریفرمر" هدایت میشود . دراین كوره گازهای هیدروكربوری با بخار آب در مجاورت كاتالیزور نیكل واكنش داده و به هیدروژن ، منواكسید كربن و دی اكسید كربن تبدیل میشود . در مراحل بعد در مجاورت كاتالیزور دیگــری تقریباً تمام حجـم گاز منواكسید كربن به گاز دی اكسید كربن تبدیل شده و سپس از جریان گاز هیــدروژن ، دی اكسید كربن در برج جذب در تماس با محلول آمین حذف می گردد. بدین ترتیب هیدروژن با درجه خلوص 94 درصد تهیه و به واحدهای مصرف كننده منتقل می شود . ظرفیت طراحی این واحد 34 میلیون فوت مكعب گاز هیدروژن در روز میباشد. لازم بذكر است با توجه به تولید هیدروژن با خلوص بالا در واحد بنزین سازی جدید امكان از سرویس خارج كردن واحد هیدروژن سازی مقدور می باشد.
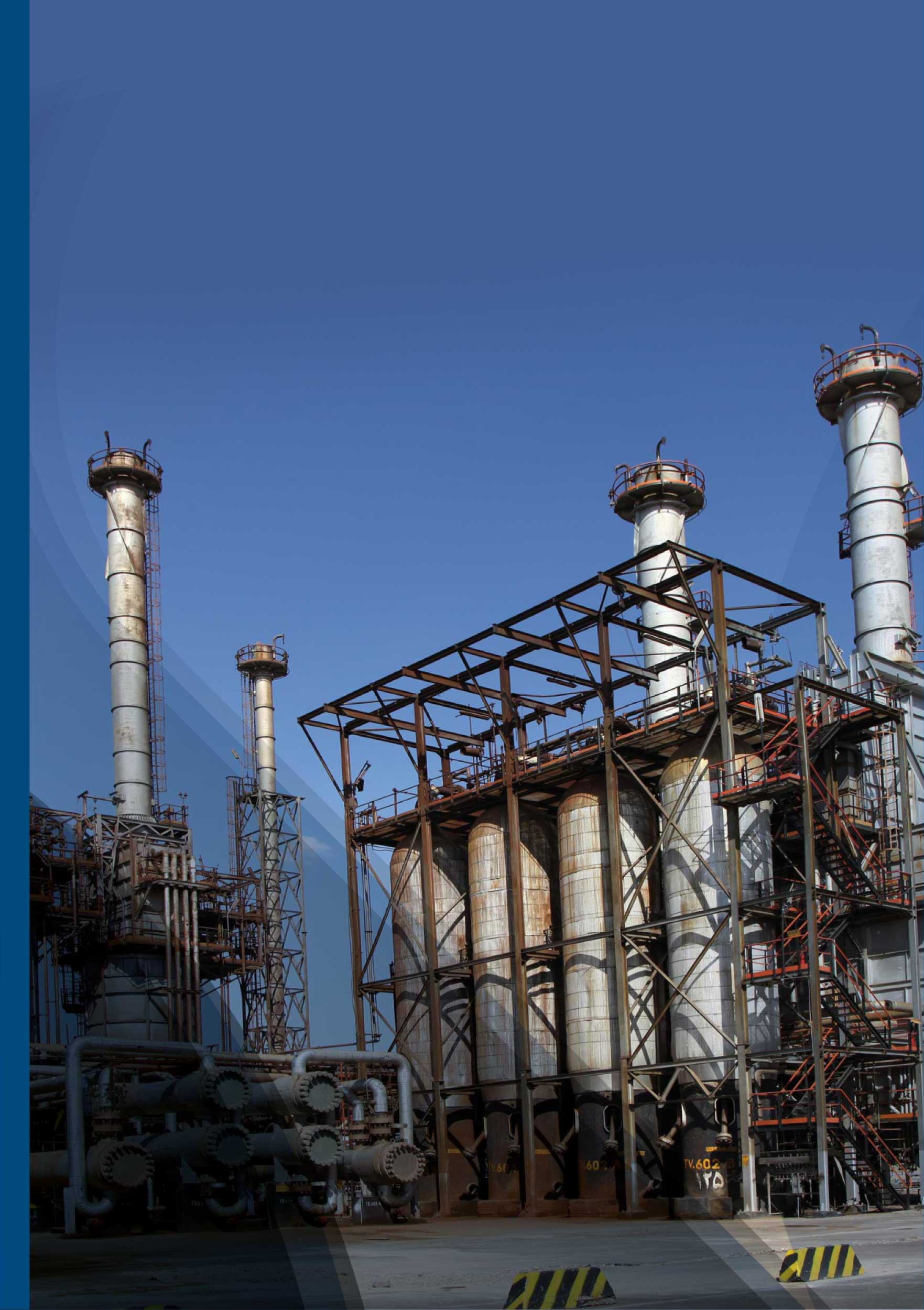
وظیفه واحد آیزوماکس تبدیل برش آیزوفید (Isofeed) به فرآورده های مفیدی نظیر نفتا ، نفت سفید و نفت گاز سبک است. آیزوفید (Isofeed) حاصل از تقطیر در خلاء،پس از خروج از این برج خوراك واحد را تشکیل می دهد. در این واحد خوراك ابتدا با "گاز هیدروژن" مخلوط و پس از گرم شدن در كوره تحت درجه حرارت معین و فشار زیاد وارد راكتور می شود و در مجاورت كاتالیزور (نیكل ، مولیبدن و... ) مولكولهای سنگین شكسته شده و مواد نیتروژنی وگوگردی آن با هیدروژن ترکیب و به گاز آمونیاک و سولفید هیدروژن تبدیل میشود. محصولات این فعل و انفعالات پس از خروج از راکتورها به قسمت تفکیک ارسال می گردند. در برج های این قسمت گازهای سبك ، بوتان ، نفتای سبک و سنگین، نفت سفید و نفت گاز از یکدیگرجدا می شوند . نفتای سنگین حاصل، جهت اصلاح درجه آرام سوزی به واحدهای بنزین سازی و یا مخازن ارسال و نفتای سبك برای اختلاط با محصول نهائی بنزین استفاده می شود. نفت سفید و نفت گاز واحد آیزوماكس بسیار مرغوب است و پس از اختلاط با نفت سفید و نفت گاز واحد تقطیر به صورت محصولات نهائی عرضه می شود. خاطر نشان می گردد نفت سفید واحد آیزوماكس در تهیه سوخت هواپیما (ATK) مورد استفاده قرار می گیرد. بخشی از خوراك كه به مواد سبكتر شكسته نشده اند با آیزوفید مخلوط و مجدداً تحت واكنش هیدروكراكینگ قرار می گیرند و مازاد آن به عنوان محصول آیزوریسایكل قابل عرضه می باشد. هیدروژن مورد نیاز این واحد از طریق واحد هیدروژن سازی یا واحد بنزین سازی جدید تامین می شود. ظرفیت طراحی واحد آیزوماكس 18 هزار بشكه در روز است.
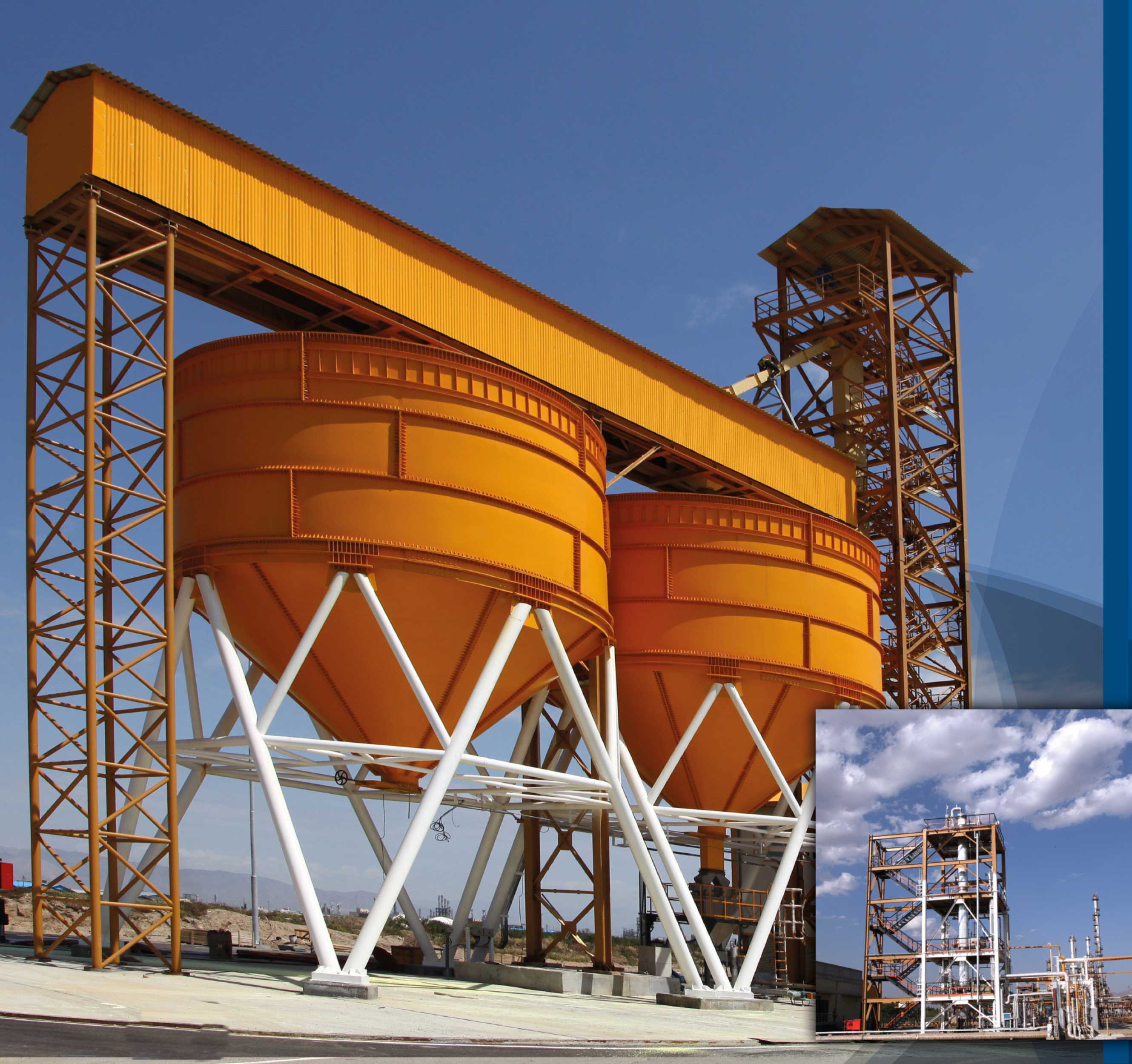
واحد تولید گرانول گوگرد با هدف صیانت از محیط زیست و جلوگیری از انتشار گوگرد جامد با ظرفیت 8 الی 18 تن گوگرد گرانول در ساعت احداث شده است . خوراك این واحد از گوگرد مذاب تولیدی در واحد گوگردسازی تأمین می گردد. تولید گرانول بر اساس فرآیند هسته گذاری اولیه بوسیله اسپری همزمان گوگرد مذاب و آب و فرآیند رشد دانه بندی در دستگاه گرانول ساز دوار انجام می پذیرد . محصول خروجی این واحد دانه های گوگرد با قطر 2 تا 6 میلیمتر می باشد كه بصورت bagging و یا فله به بازار عرضه می گردد .
وظیفه این واحد بازیابی گازهای ارسالی به فلر و در نهایت تزریق این گاز به شبكه سوخت پالایشگاه می باشد. این واحد در اصل جزء واحدهای با كاركرد زیست محیطی می باشد كه قادر است به راحتی بیش از 13 میلیون نرمال متر مكعب گازهای ارسالی از واحدها به فلر را دریافت، تصفیه، جداسازی و بازیابی كند. ظرفیت طراحی این واحد دریافت 1535 نرمال متر مكعب در ساعت گاز و تولید 1380 نرمال متر مكعب در ساعت گاز و همچنین تولید مقداری نفتای سبك با توجه به ماهیت متغیر گازهای ورودی به واحد می باشد. این واحد شامل دو ردیف كمپرسور می باشد كه توانائی فشردن گازها تا فشار km/cm2 6 و سپس تصفیه گازهای اسیدی توسط برج جذب آمین می باشد . با راه اندازی این واحد از انتشار سالانه بیش از 50 هزار تن گاز دی اكسید كربن و سوختن سالانه بیش از 700 تن گاز اسیدی H2S جلوگیری بعمل آمده است .
واحد تولید گرانول گوگرد با هدف صیانت از محیط زیست و جلوگیری از انتشار گوگرد جامد با ظرفیت 8 الی 18 تن گوگرد گرانول در ساعت احداث شده است . خوراك این واحد از گوگرد مذاب تولیدی در واحد گوگردسازی تأمین می گردد. تولید گرانول بر اساس فرآیند هسته گذاری اولیه بوسیله اسپری همزمان گوگرد مذاب و آب و فرآیند رشد دانه بندی در دستگاه گرانول ساز دوار انجام می پذیرد . محصول خروجی این واحد دانه های گوگرد با قطر 2 تا 6 میلیمتر می باشد كه بصورت bagging و یا فله به بازار عرضه می گردد .
وظیفه این واحد بازیابی گازهای ارسالی به فلر و در نهایت تزریق این گاز به شبكه سوخت پالایشگاه می باشد. این واحد در اصل جزء واحدهای با كاركرد زیست محیطی می باشد كه قادر است به راحتی بیش از 13 میلیون نرمال متر مكعب گازهای ارسالی از واحدها به فلر را دریافت، تصفیه، جداسازی و بازیابی كند. ظرفیت طراحی این واحد دریافت 1535 نرمال متر مكعب در ساعت گاز و تولید 1380 نرمال متر مكعب در ساعت گاز و همچنین تولید مقداری نفتای سبك با توجه به ماهیت متغیر گازهای ورودی به واحد می باشد. این واحد شامل دو ردیف كمپرسور می باشد كه توانائی فشردن گازها تا فشار km/cm2 6 و سپس تصفیه گازهای اسیدی توسط برج جذب آمین می باشد . با راه اندازی این واحد از انتشار سالانه بیش از 50 هزار تن گاز دی اكسید كربن و سوختن سالانه بیش از 700 تن گاز اسیدی H2S جلوگیری بعمل آمده است .
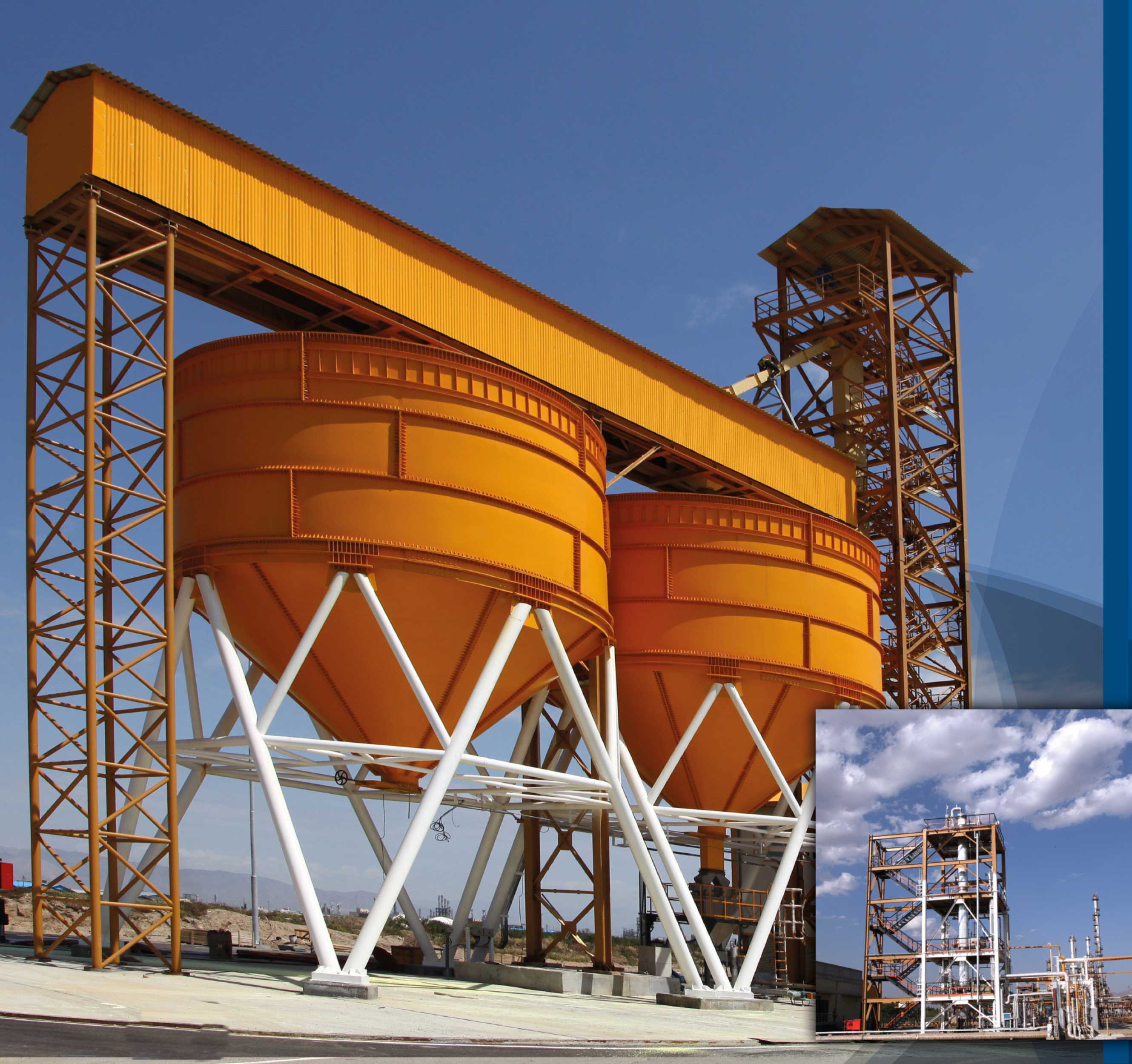
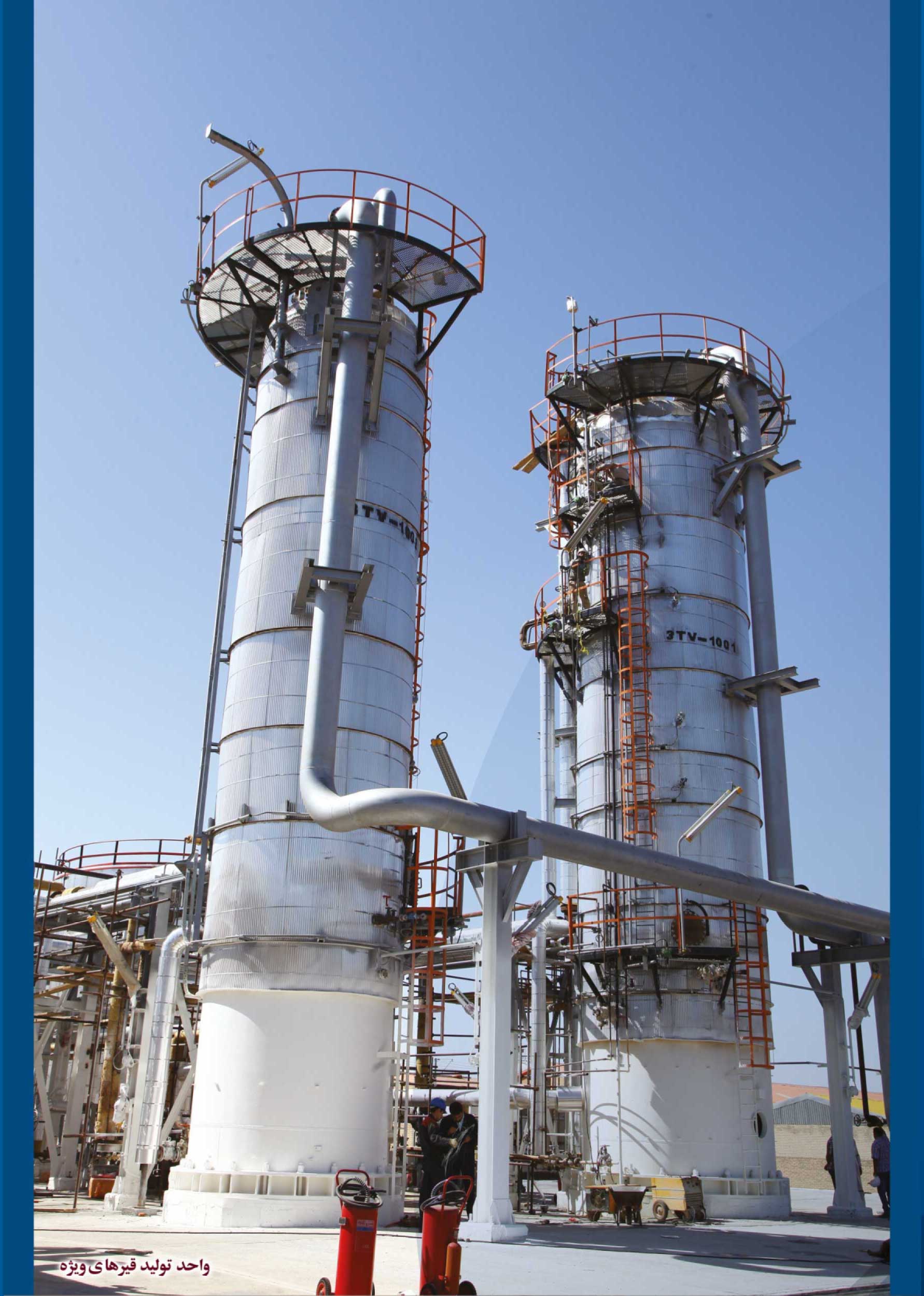
گازهای حاصل از واحدهای گوگرد زدایی از نفتا ، کاهش گرانروی ، گوگردزدائی نفت گاز و آیزوماکس که حاوی گازهای اسیدی سولفید هیدروژن است ابتدا باید در این واحد مورد تصفیه قرار گیرند. بدین ترتیب که در برجهای جذب کننده این واحد که در فشارهای مختلف (بالا ، متوسط و پایین) در سرویس هستند، گازهای سولفید هیدروژن توسط محلول منواتانول آمین جذب و گازهای تصفیه شده از بالای برجها خارج می شوند. گازهای تصفیه شده فشار بالا به واحد هیدروژن ، گازهای تصفیه شده فشار متوسط به واحد گاز مایع و گازهای تصفیه شده فشار پایین به شبكه سوخت گازی پالایشگاه انتقال می یابد. در برج احیاء ، گازهای سولفید هیدروژن که جذب محلول آمین گردیده از آن جدا و جهت تولید گوگرد به واحد گوگردسازی منتقل می گردد. ظرفیت طراحی این واحد 5/11 میلیون فوت مكعب در روز است.
وظیفه این واحد تصفیه آب ترش ویا به عبارت دیگر جدا نمودن آمونیاک و سولفید هیدروژن محلول در آبهای فرایندی میباشد . آب استحصالی از فرآیند تولید برخی واحدها به منظور جداسازی سولفید هیدروژن و آمونیاك موجود در آن به واحد تصفیه آب ترش هدایت می شود این واحد از طریق دو برج ؛ آمونیاک و سولفید هیدروژن موجود در آبهای فرایندی را جدا نموده و در نهایت آب تصفیه شده جهت استفاده در بخش نمک زدا به واحد تقطیر انتقال یافته و گازهای سولفید هیدروژن وآمونیاک خروجی از این واحد، به واحد گوگردسازی انتقال می یابد. این واحد جهت تصفیه 38 مترمكعب در ساعت آب ترش طراحی گردیده است.
كلیه گازهای خروجی از واحد تصفیه گاز با آمین و واحد آب ترش ، به عنوان خوراك، به این واحد منتقل شده و به روش "كلاوس" به گوگرد جامد تبدیل می شوند. در این واحد ابتدا خوراك در یك كوره مخصوص و در حرارت بالای 1200 درجه سانتیگراد تحت تبدیل حرارتی قرار گرفته و سپس در مجاورت كاتالیزور در یك راكتور دو مرحله ای به گوگرد مذاب تبدیل و پس از تبدیل شدن به گوگرد جامد به بازار عرضه می شود. این واحد جهت تولید روزانه 81 تن گوگرد طراحی شده است.
این واحد با هدف تولید قیرهای گوگردی ، پلیمری ، انواع قیرهای امولسیونی و قیرهای MCو RC احداث شده است . خوراک این واحد قسمتی از ته مانده برج تقطیر در خلا است که در درجه حرارت معینی با دمیدن هوا اکسید شده و پس از اضافه کردن مواد افزودنی در شرایط خاص محصول قیر ویژه با كیفیت مناسب تهیه می شود. ضمناً این واحد مجهز به دستگاه پکیج بسته بندی می باشد. ظرفیت طراحی این واحد 5000 بشكه در روز است.
گازهای حاصل از واحدهای گوگرد زدایی از نفتا ، کاهش گرانروی ، گوگردزدائی نفت گاز و آیزوماکس که حاوی گازهای اسیدی سولفید هیدروژن است ابتدا باید در این واحد مورد تصفیه قرار گیرند. بدین ترتیب که در برجهای جذب کننده این واحد که در فشارهای مختلف (بالا ، متوسط و پایین) در سرویس هستند، گازهای سولفید هیدروژن توسط محلول منواتانول آمین جذب و گازهای تصفیه شده از بالای برجها خارج می شوند. گازهای تصفیه شده فشار بالا به واحد هیدروژن ، گازهای تصفیه شده فشار متوسط به واحد گاز مایع و گازهای تصفیه شده فشار پایین به شبكه سوخت گازی پالایشگاه انتقال می یابد. در برج احیاء ، گازهای سولفید هیدروژن که جذب محلول آمین گردیده از آن جدا و جهت تولید گوگرد به واحد گوگردسازی منتقل می گردد. ظرفیت طراحی این واحد 5/11 میلیون فوت مكعب در روز است.
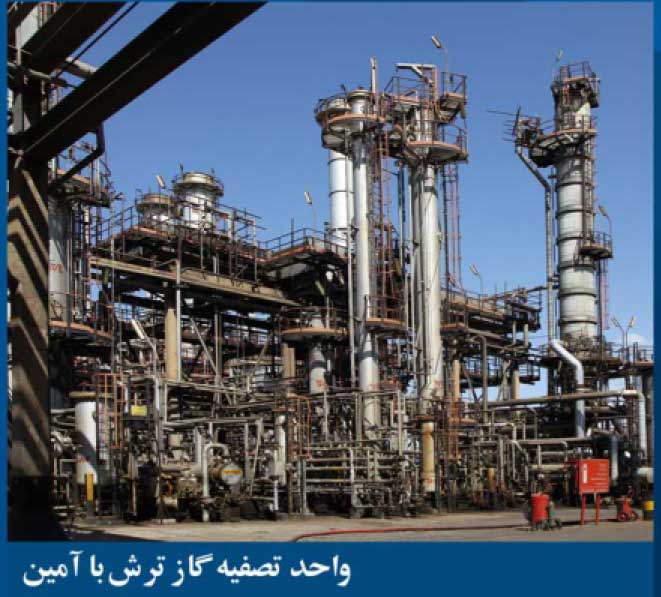
وظیفه این واحد تصفیه آب ترش ویا به عبارت دیگر جدا نمودن آمونیاک و سولفید هیدروژن محلول در آبهای فرایندی میباشد . آب استحصالی از فرآیند تولید برخی واحدها به منظور جداسازی سولفید هیدروژن و آمونیاك موجود در آن به واحد تصفیه آب ترش هدایت می شود این واحد از طریق دو برج ؛ آمونیاک و سولفید هیدروژن موجود در آبهای فرایندی را جدا نموده و در نهایت آب تصفیه شده جهت استفاده در بخش نمک زدا به واحد تقطیر انتقال یافته و گازهای سولفید هیدروژن وآمونیاک خروجی از این واحد، به واحد گوگردسازی انتقال می یابد. این واحد جهت تصفیه 38 مترمكعب در ساعت آب ترش طراحی گردیده است.
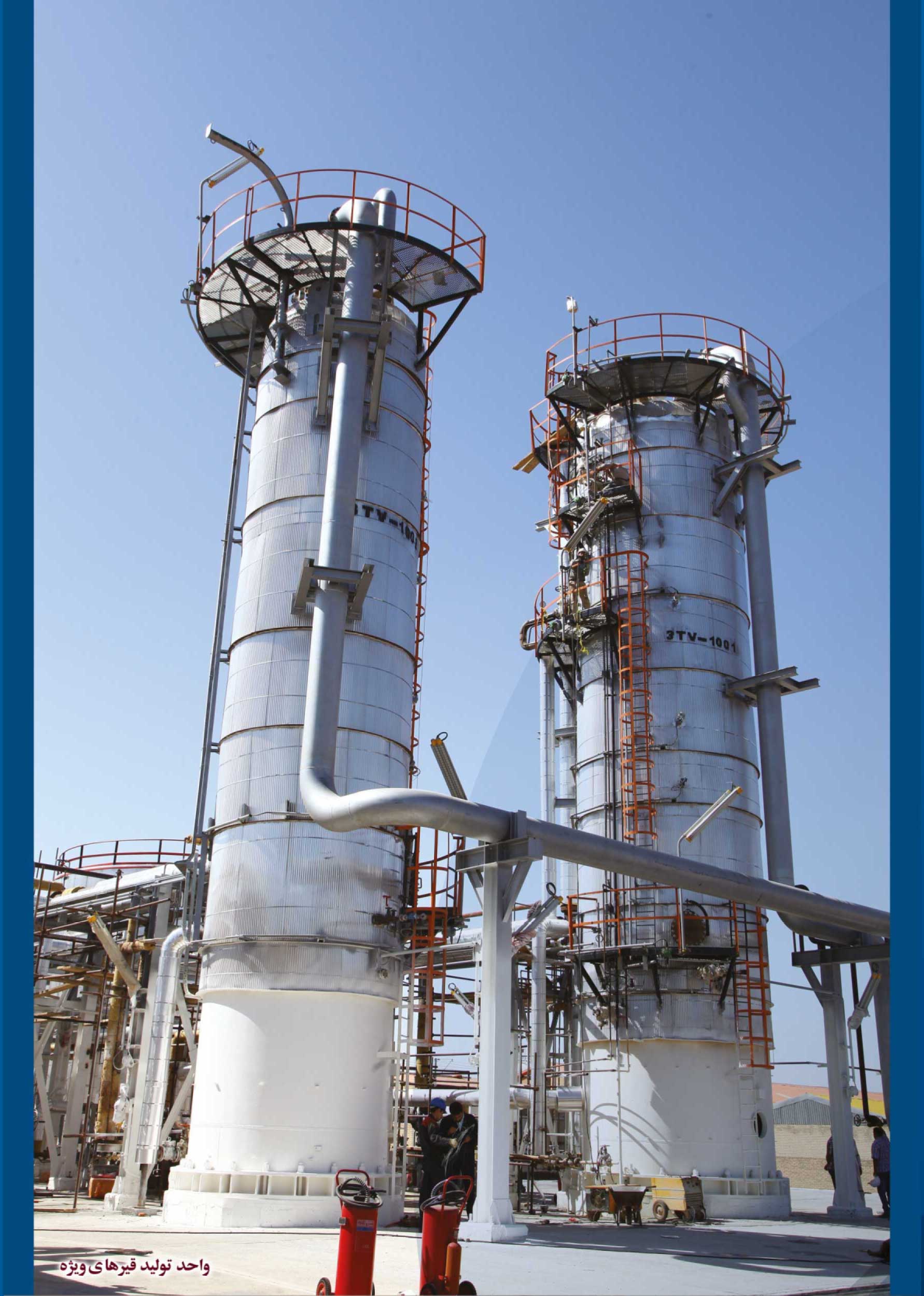
كلیه گازهای خروجی از واحد تصفیه گاز با آمین و واحد آب ترش ، به عنوان خوراك، به این واحد منتقل شده و به روش "كلاوس" به گوگرد جامد تبدیل می شوند. در این واحد ابتدا خوراك در یك كوره مخصوص و در حرارت بالای 1200 درجه سانتیگراد تحت تبدیل حرارتی قرار گرفته و سپس در مجاورت كاتالیزور در یك راكتور دو مرحله ای به گوگرد مذاب تبدیل و پس از تبدیل شدن به گوگرد جامد به بازار عرضه می شود. این واحد جهت تولید روزانه 81 تن گوگرد طراحی شده است.
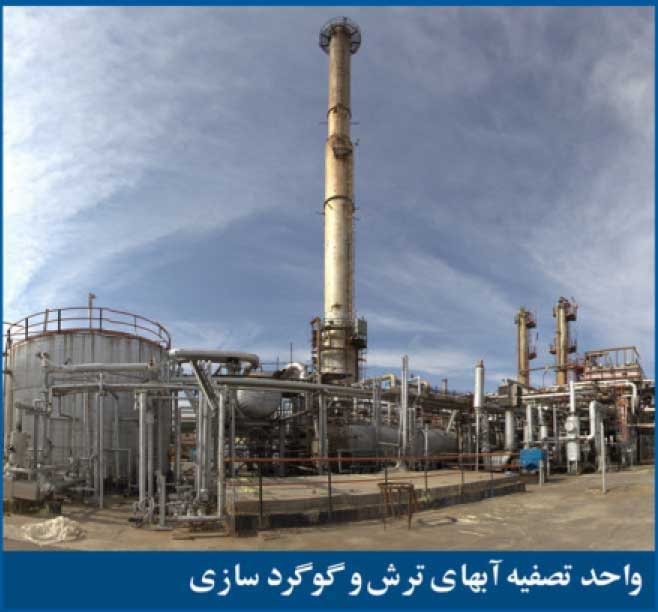
این واحد با هدف تولید قیرهای گوگردی ، پلیمری ، انواع قیرهای امولسیونی و قیرهای MCو RC احداث شده است . خوراک این واحد قسمتی از ته مانده برج تقطیر در خلا است که در درجه حرارت معینی با دمیدن هوا اکسید شده و پس از اضافه کردن مواد افزودنی در شرایط خاص محصول قیر ویژه با كیفیت مناسب تهیه می شود. ضمناً این واحد مجهز به دستگاه پکیج بسته بندی می باشد. ظرفیت طراحی این واحد 5000 بشكه در روز است.
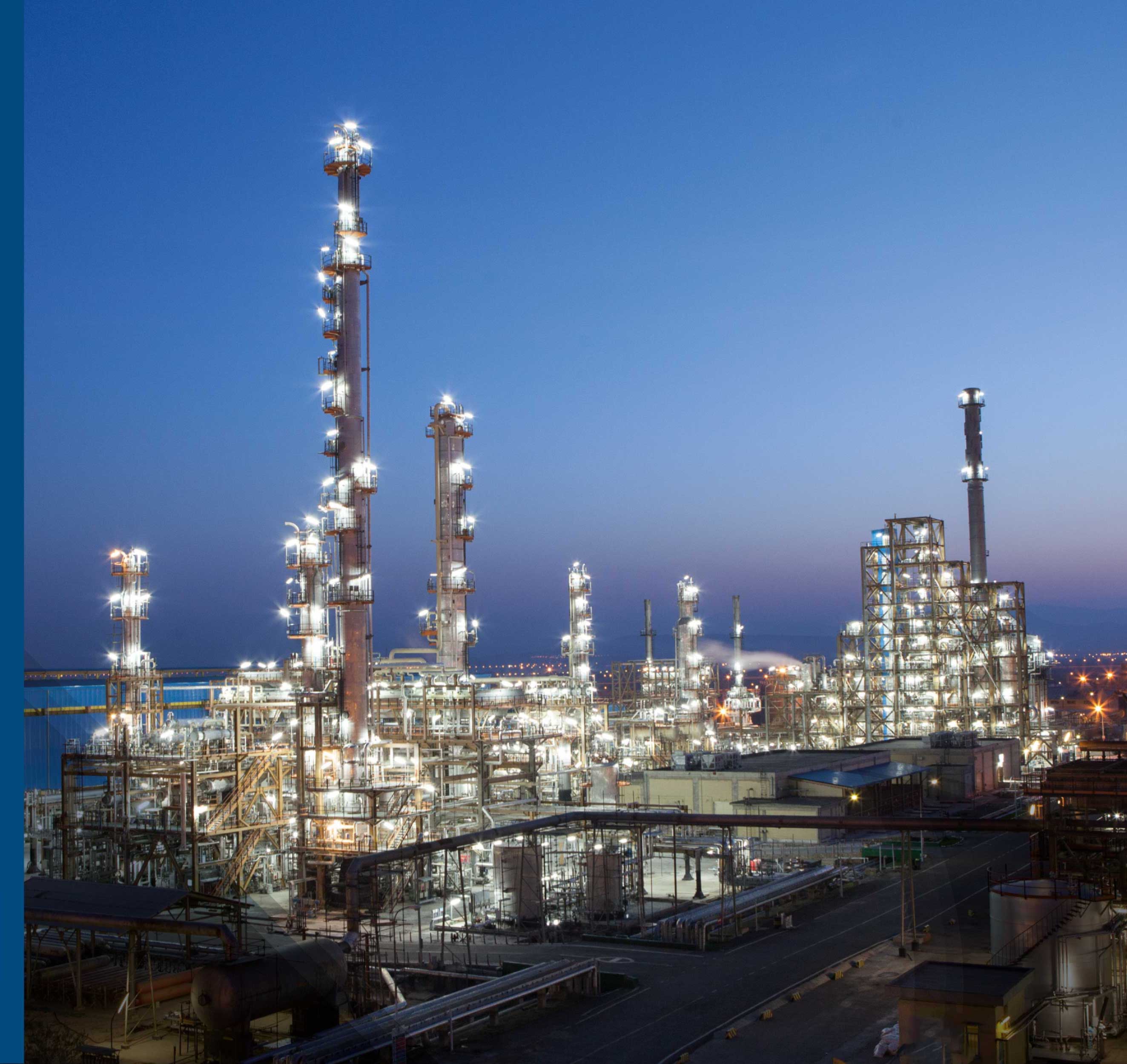
این واحد بمنظور افزایش درجه آرام سوزی بنزین تولیدی و بالابردن اكتان بنزین ایجاد شده است. در این واحد كاتالیست بطور مداوم احیاء می گردد. خوراك این واحد نفتای سنگین دریافتی از واحد تقطیر در جو و یا خط لوله است كه پس از تصفیه هیدروژنی وارد بخش اكتان افزا شده و پس از واكنشهای تبدیل كاتالیستی در سه راكتور به محصول هیدروژن با خلوص بالا ، گاز مایع و محصول Reformate با عدد اكتان حدود 100 تبدیل می شود محصول هیدروژن به شبكه هیدروژن پالایشگاه ،گاز مایع به واحد استحصال گاز مایع و محصول Reformate جهت جداسازی بنزن به واحد استخراج بنزن انتقال می یابد. لازم به ذكر است با توجه به پایین بودن ظرفیت تولید واحد بنزین سازی قدیم و لزوم ارتقاء كیفیت بنزین تولیدی و با در نظر گرفتن پتانسیلهای آتی تولید نفتا در شركت ، واحد بنزین سازی جدید در این شركت احداث گردیده است. محصول نهائی این واحد جهت اختلاط و تولید بنزین نهایی به بخش مخازن منتقل می شود. ظرفیت طراحی این واحد 20000 بشكه در روز می باشد.
وظیفه این واحد استخراج بنزن موجود در بنزین جهت انطباق آن با مشخصات بنزین استاندارد EU-V می باشد . بدین منظور محصول Reformate دریافت شده از واحد اكتان افزا دارای حدود 4.7 درصد حجمی بنزن می باشد كه سبب آلودگی محیط زیست می شود . در این واحد میزان بنزن تا حد استاندارد EU-V (كمتر از 1% حجمی) كاهش می یابد و بنزن تولیدی با خلوص بالا به عنوان خوراك به شركتهای پتروشیمی قابل عرضه می باشد . ظرفیت طراحی این واحد 90 تن (750 بشكه) در روز بنزن می باشد .
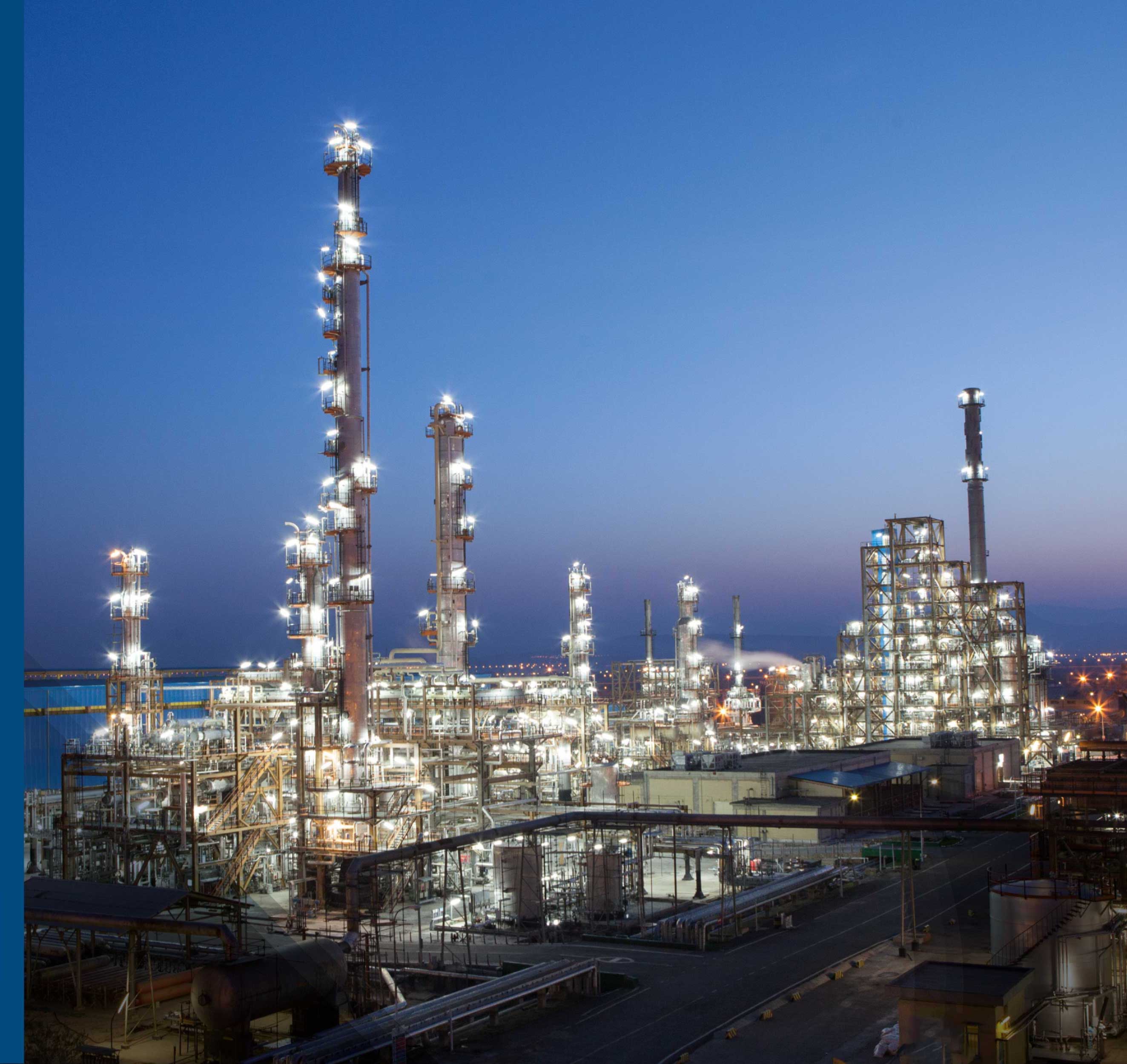
این واحد بمنظور افزایش درجه آرام سوزی بنزین تولیدی و بالابردن اكتان بنزین ایجاد شده است. در این واحد كاتالیست بطور مداوم احیاء می گردد. خوراك این واحد نفتای سنگین دریافتی از واحد تقطیر در جو و یا خط لوله است كه پس از تصفیه هیدروژنی وارد بخش اكتان افزا شده و پس از واكنشهای تبدیل كاتالیستی در سه راكتور به محصول هیدروژن با خلوص بالا ، گاز مایع و محصول Reformate با عدد اكتان حدود 100 تبدیل می شود محصول هیدروژن به شبكه هیدروژن پالایشگاه ،گاز مایع به واحد استحصال گاز مایع و محصول Reformate جهت جداسازی بنزن به واحد استخراج بنزن انتقال می یابد. لازم به ذكر است با توجه به پایین بودن ظرفیت تولید واحد بنزین سازی قدیم و لزوم ارتقاء كیفیت بنزین تولیدی و با در نظر گرفتن پتانسیلهای آتی تولید نفتا در شركت ، واحد بنزین سازی جدید در این شركت احداث گردیده است. محصول نهائی این واحد جهت اختلاط و تولید بنزین نهایی به بخش مخازن منتقل می شود. ظرفیت طراحی این واحد 20000 بشكه در روز می باشد.
وظیفه این واحد استخراج بنزن موجود در بنزین جهت انطباق آن با مشخصات بنزین استاندارد EU-V می باشد . بدین منظور محصول Reformate دریافت شده از واحد اكتان افزا دارای حدود 4.7 درصد حجمی بنزن می باشد كه سبب آلودگی محیط زیست می شود . در این واحد میزان بنزن تا حد استاندارد EU-V (كمتر از 1% حجمی) كاهش می یابد و بنزن تولیدی با خلوص بالا به عنوان خوراك به شركتهای پتروشیمی قابل عرضه می باشد . ظرفیت طراحی این واحد 90 تن (750 بشكه) در روز بنزن می باشد .
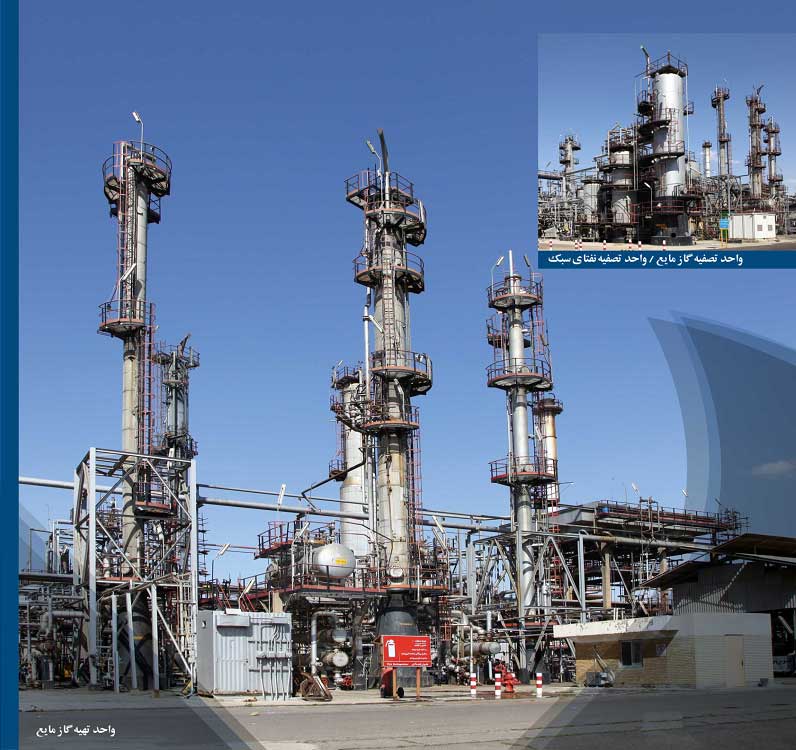
گازهای سبكی كه از واحد تقطیر نفت خام ، تبدیل كاتالیستی ، واحد تصفیه گاز با آمین ، آیزوماكس و بنزین سازی جدید به دست می آید عمدتاً مخلوطی از متان ، اتان، پروپان ، بوتان و اندكی پنتان است. در این واحد ابتدا مواد نفتی سنگین تر از گاز مایع (نفتای سبك) در برج تثبیت كننده جدا شده و سپس گازهای متان و اتان بوسیله عمل تفكیك از سایر گازها مجزا شده و در مراحل بعدی نیز پروپان و بوتان از یكدیگر جدا می شوند . آنگاه گاز مایع با اختلاط پروپان و بوتان به نسبتهای مناسب تهیه می شود. گاز مایعی كه به بازار عرضه می گردد مخلوطی از پروپان و بوتان است كه نسبت حجمی اختلاط آنها در فصول مختلف سال متغییر است. به عبارتی پروپان كه سبك تر است در تابستان كمتر و در زمستان بیشتر است. ظرفیت طراحی شده واحد تهیه گاز مایع 6000 بشكه در روز است.
گاز مایع تولیدی در واحد استحصال گاز مایع حاوی مقادیر اندكی تركیبات گوگردی نظیر سولفید هیدروژن و مركاپتانهای سبك است. در این واحد تركیبات سولفید هیدروژن ومركاپتانهای موجود در گاز مایع بعد از تماس با محلول كاستیك تحت عملیات اكسیداسیون قرارگرفته و مركاپتانها به دی سولفید ها تبدیل شده و از گاز مایع جدا می شود. ظرفیت طراحی این واحد 4500 بشكه در روز است.
نفتای سبك تولیدی از واحد گاز مایع نیز حاوی مقادیر جزئی تركیبات گوگردی و عمدتا بصورت مركاپتانهای سبك می باشد. در این واحد نفتای سبك پس از عبور از محلول كاستیك ، وارد رآكتور اكسیداسیون شده و مركاپتانهای موجود تبدیل به دی سولفیدها می شوند. ظرفیت طراحی این واحد 6000 بشكه در روز است.
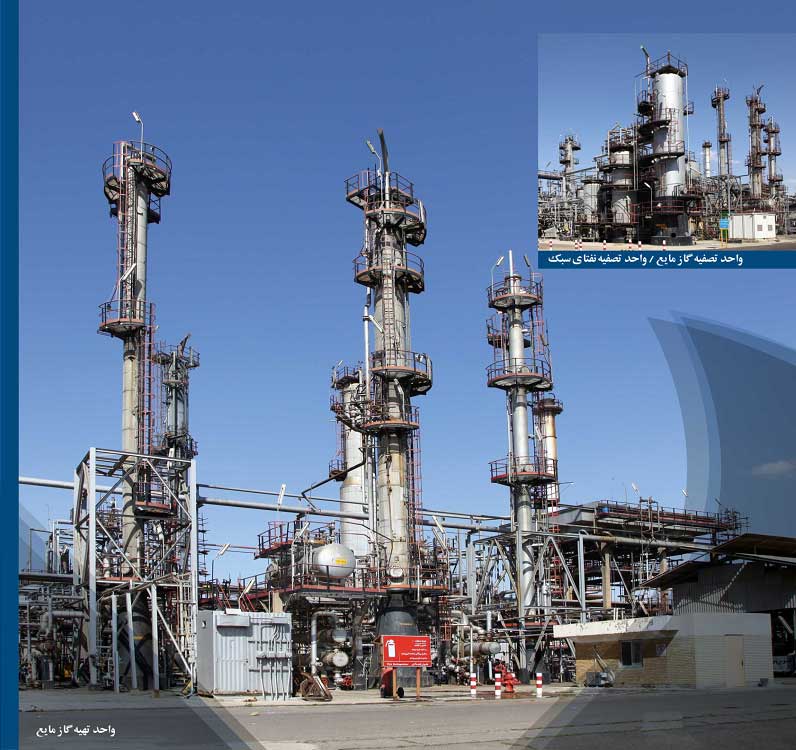
گازهای سبكی كه از واحد تقطیر نفت خام ، تبدیل كاتالیستی ، واحد تصفیه گاز با آمین ، آیزوماكس و بنزین سازی جدید به دست می آید عمدتاً مخلوطی از متان ، اتان، پروپان ، بوتان و اندكی پنتان است. در این واحد ابتدا مواد نفتی سنگین تر از گاز مایع (نفتای سبك) در برج تثبیت كننده جدا شده و سپس گازهای متان و اتان بوسیله عمل تفكیك از سایر گازها مجزا شده و در مراحل بعدی نیز پروپان و بوتان از یكدیگر جدا می شوند . آنگاه گاز مایع با اختلاط پروپان و بوتان به نسبتهای مناسب تهیه می شود. گاز مایعی كه به بازار عرضه می گردد مخلوطی از پروپان و بوتان است كه نسبت حجمی اختلاط آنها در فصول مختلف سال متغییر است. به عبارتی پروپان كه سبك تر است در تابستان كمتر و در زمستان بیشتر است. ظرفیت طراحی شده واحد تهیه گاز مایع 6000 بشكه در روز است.
گاز مایع تولیدی در واحد استحصال گاز مایع حاوی مقادیر اندكی تركیبات گوگردی نظیر سولفید هیدروژن و مركاپتانهای سبك است. در این واحد تركیبات سولفید هیدروژن ومركاپتانهای موجود در گاز مایع بعد از تماس با محلول كاستیك تحت عملیات اكسیداسیون قرارگرفته و مركاپتانها به دی سولفید ها تبدیل شده و از گاز مایع جدا می شود. ظرفیت طراحی این واحد 4500 بشكه در روز است.
نفتای سبك تولیدی از واحد گاز مایع نیز حاوی مقادیر جزئی تركیبات گوگردی و عمدتا بصورت مركاپتانهای سبك می باشد. در این واحد نفتای سبك پس از عبور از محلول كاستیك ، وارد رآكتور اكسیداسیون شده و مركاپتانهای موجود تبدیل به دی سولفیدها می شوند. ظرفیت طراحی این واحد 6000 بشكه در روز است.
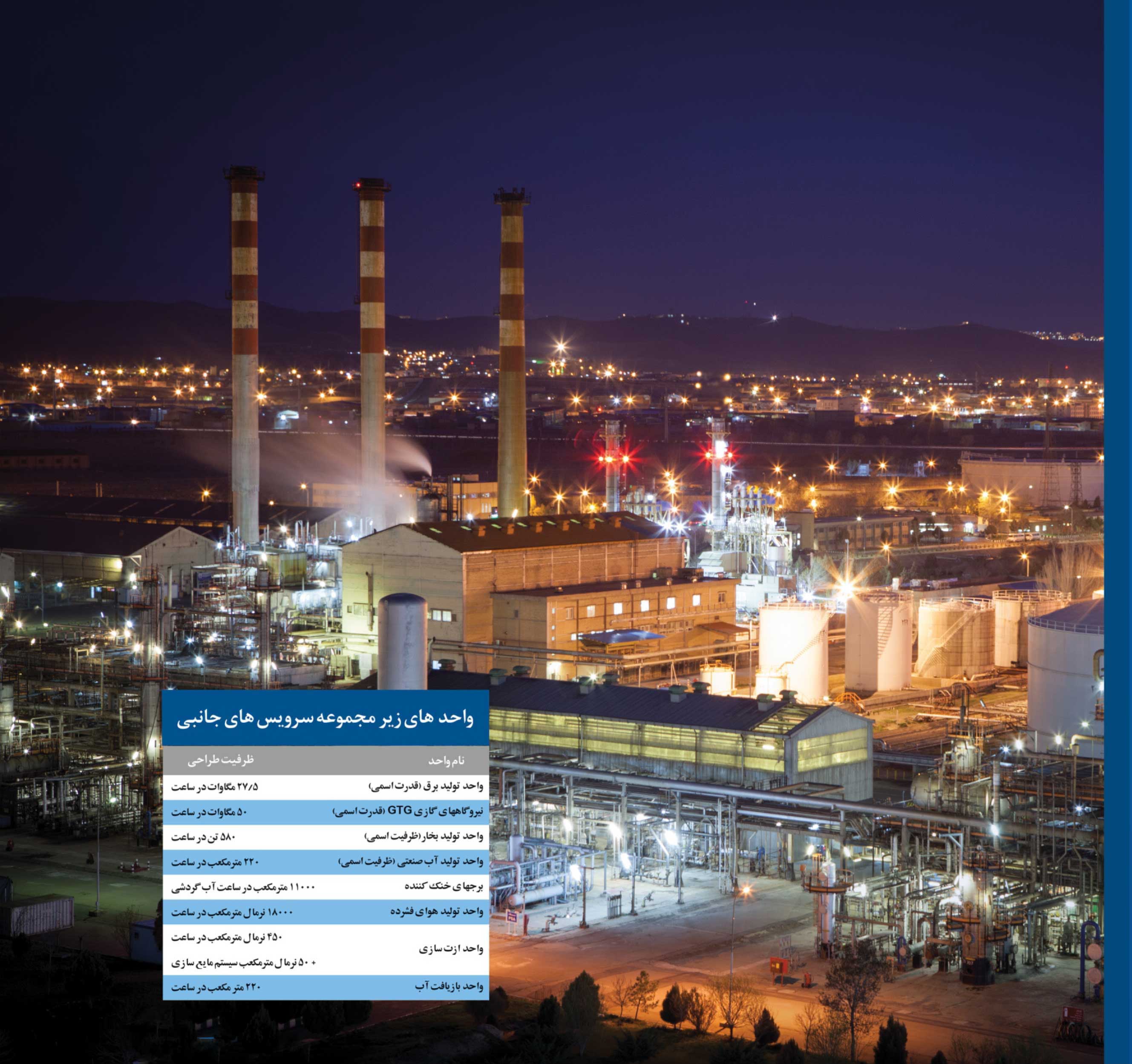
برای پشتیبانی واحدهای پالایشی مجموعه سرویسهای آب و برق و بخار (سرویسهای جانبی) طراحی شده اند كه به شرح ذیل عملیات پشتیبانی را انجام می دهند.
- تولید برق سیستم تولید برق شركت پالایش نفت تبریز از دو بخش نیروگاه قدیم و جدید تشكیل شده است نیروگاه قدیم از سه توبین بخار كه با توان تولید (ظرفیت اسمی) 5/27 مگاوات (مجموعاً) تشكیل شده است كه شامل دو مولد 10 مگاواتی و یك مولد 5/7 مگاواتی می باشد. نیروگاه جدید از دو مولد GTG (توربین گازی) با ظرفیت اسمی هر مولد 7/24 مگاوات تشكیل شده است نیروگاههای جدید و قدیم با 2 خط ارتباطی به هم لینك شده اند كه امكان تبادل 14 مگاوات برق مابین دو نیروگاه وجود دارد.
- تولید بخار واحد تولید بخاربمنظور تامین بخار مورد نیاز توربین ها، مولدهای برق و واحدهای پالایشی از دو بخش دیگهای بخار قدیم و سیستم HRSG (سیستم بازیافت حرارتی) تشكیل شده است تعداد دیگهای بخار 5 دستگاه می باشد كه ظرفیت اسمی هر یك 102 تن در ساعت و ظرفیت تولید بخار توسط دو دستگاه HRSG جمعاً 80 تن در ساعت می باشد. لازم بذکر است قسمت بخار سازی واحد بنزین سازی جدید نیز ظرفیت تولید 30 تن در ساعت بخار را دارا میباشد و در مجموع ظرفیت اسمی تولید بخار 620 تن در ساعت می باشد.
برای پشتیبانی واحدهای پالایشی مجموعه سرویسهای آب و برق و بخار (سرویسهای جانبی) طراحی شده اند كه به شرح ذیل عملیات پشتیبانی را انجام می دهند.
- تولید برق سیستم تولید برق شركت پالایش نفت تبریز از دو بخش نیروگاه قدیم و جدید تشكیل شده است نیروگاه قدیم از سه توبین بخار كه با توان تولید (ظرفیت اسمی) 5/27 مگاوات (مجموعاً) تشكیل شده است كه شامل دو مولد 10 مگاواتی و یك مولد 5/7 مگاواتی می باشد. نیروگاه جدید از دو مولد GTG (توربین گازی) با ظرفیت اسمی هر مولد 7/24 مگاوات تشكیل شده است نیروگاههای جدید و قدیم با 2 خط ارتباطی به هم لینك شده اند كه امكان تبادل 14 مگاوات برق مابین دو نیروگاه وجود دارد.
- تولید بخار واحد تولید بخاربمنظور تامین بخار مورد نیاز توربین ها، مولدهای برق و واحدهای پالایشی از دو بخش دیگهای بخار قدیم و سیستم HRSG (سیستم بازیافت حرارتی) تشكیل شده است تعداد دیگهای بخار 5 دستگاه می باشد كه ظرفیت اسمی هر یك 102 تن در ساعت و ظرفیت تولید بخار توسط دو دستگاه HRSG جمعاً 80 تن در ساعت می باشد. لازم بذکر است قسمت بخار سازی واحد بنزین سازی جدید نیز ظرفیت تولید 30 تن در ساعت بخار را دارا میباشد و در مجموع ظرفیت اسمی تولید بخار 620 تن در ساعت می باشد.
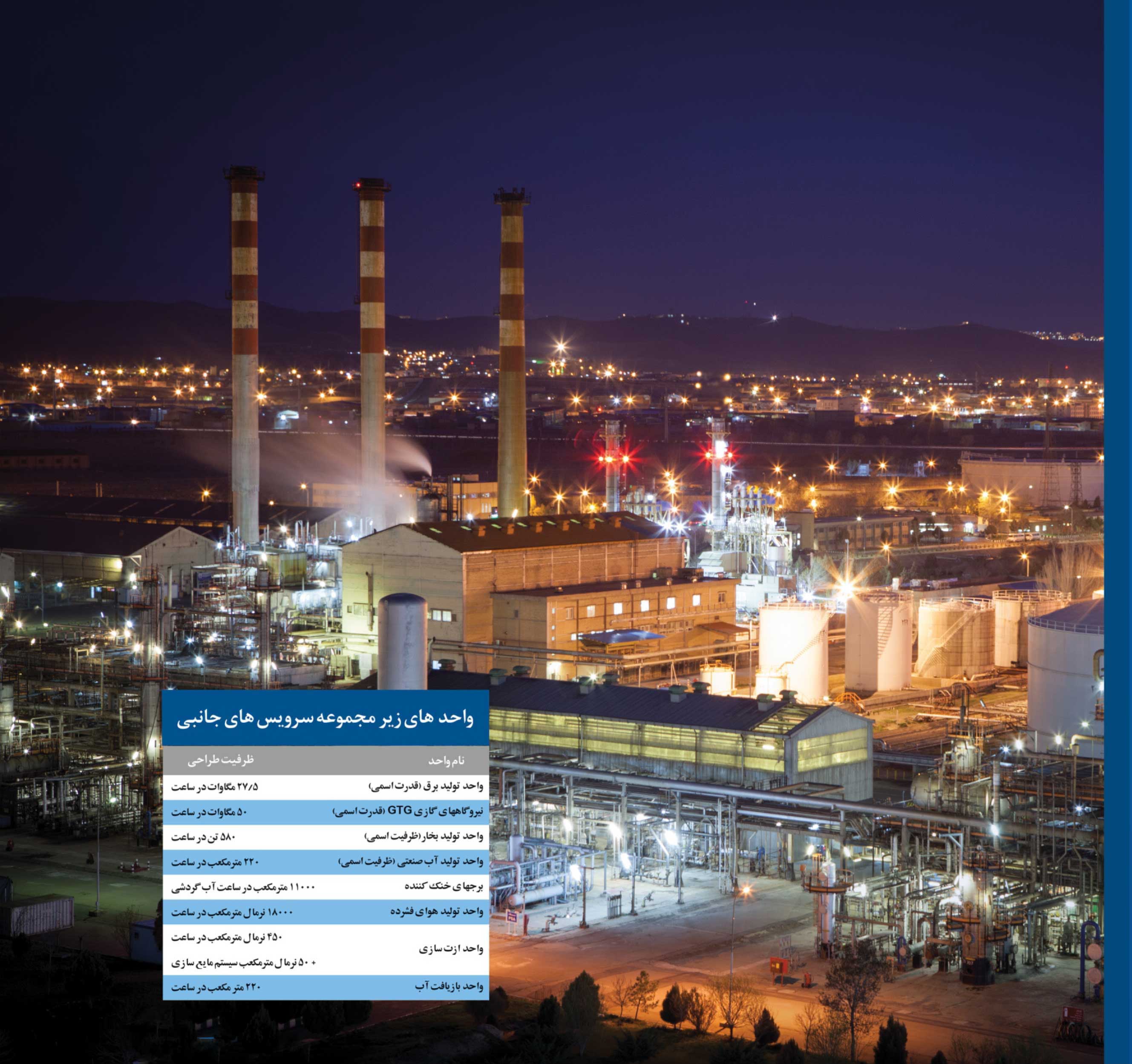
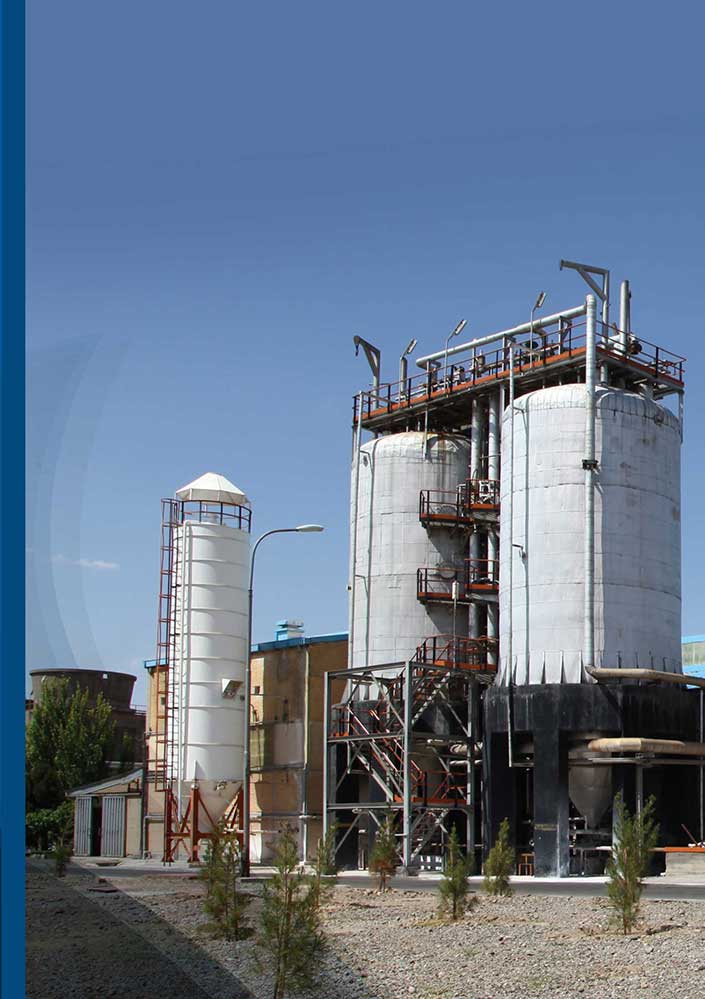
این واحد مجموعه واحدهای تولید آب صنعتی، برج خنك كننده، تولید هوای فشرده (هوای ابزار دقیق و كارگاهی) ، ازت سازی، سوخت رسانی و آب آتش نشانی ، آب آشامیدنی و آب كارگاهی و باغبانی می باشد.
- تولید آب صنعتی: دو برج فعل و انفعال با سیستم Hot Lime reaction جهت تولید آب مورد نیاز دیگهای بخار با ظرفیت اسمی 110 مترمكعب برای هر برج طراحی شده است این مجموعه شامل دو برج فعل و انفعال ، 6 عدد فیلتر زغالی و 4 عدد فیلتر رزینی جهت نرم كردن آب مورد نیاز دیگهای بخار می باشد.
- برج خنك كننده : این واحد شامل 4 دستگاه تلمبه آب چرخشی هر كدام به ظرفیت 5500 مترمكعب در ساعت و دو برج خنك كننده هركدام با هفت Cell می باشد كه عملیات خنك كردن واحدهای پالایشی توسط این مجموعه انجام می گیرد.
- تولید هوای فشرده: هوای ابزار دقیقی و صنعتی مورد نیاز بخشهای مختلف پالایشگاه در این واحد از طریق 5 دستگاه كمپرسور (یك دستگاه كمپرسور توربینی و 4 دستگاه كمپرسور برقی) تامین می شود ظرفیت تولید هوای فشرده در شرایط فعلی 18000 نرمال مترمكعب در ساعت می باشد.
- واحد تولید ازت: این واحد جهت تامین ازت مصرفی پالایشگاه برای مصارف فرآیندی و گاز پوششی مخازن ، طراحی و نصب شده است كه ظرفیت آن 450 نرمال مترمكعب در ساعت گاز ازت و 50 نرمال مترمكعب در ساعت مایع می باشد.
- سوخت رسانی: این مجموعه شامل 5 دستگاه تلمبه جهت تامین سوخت مایع مصرفی در پالایشگاه در دو بخش سوخت نفت كوره و نفتا است. سایر قسمتهای مجموعه آب صنعتی برای تامین آب آتش نشانی، آب آشامیدنی و آب كارگاهی و باغبانی طراحی شده اند.
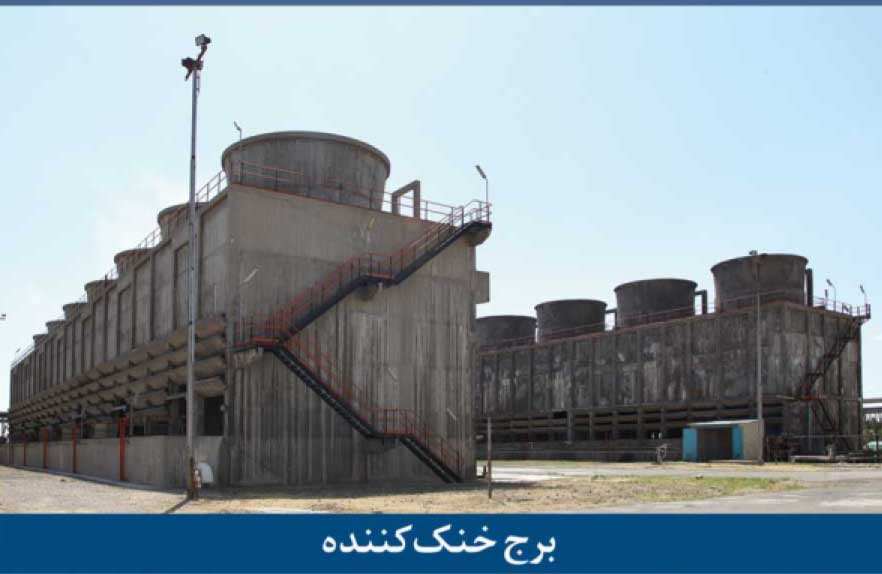
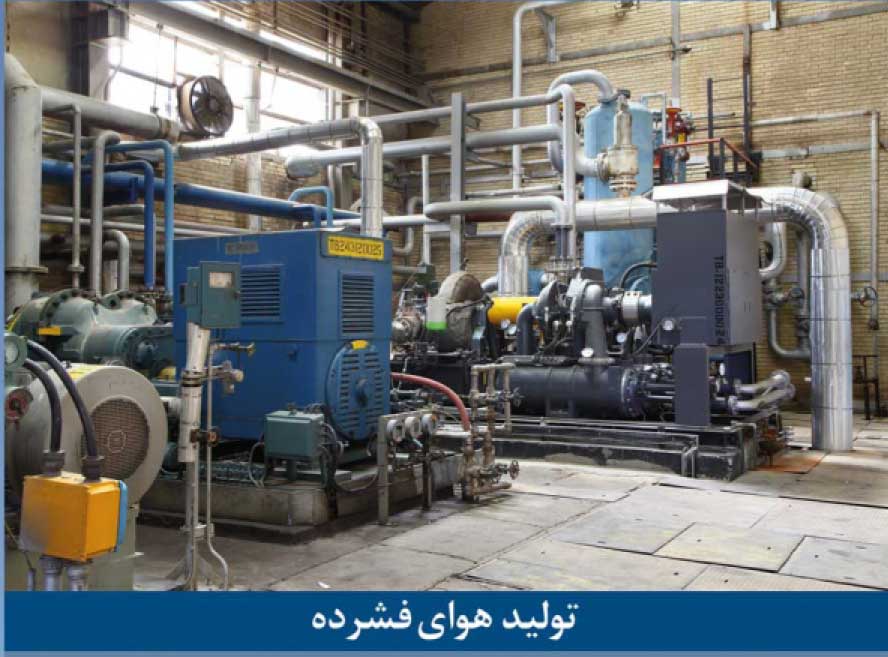
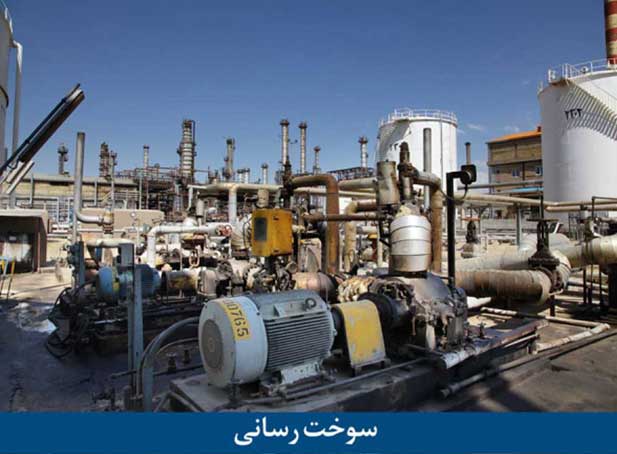
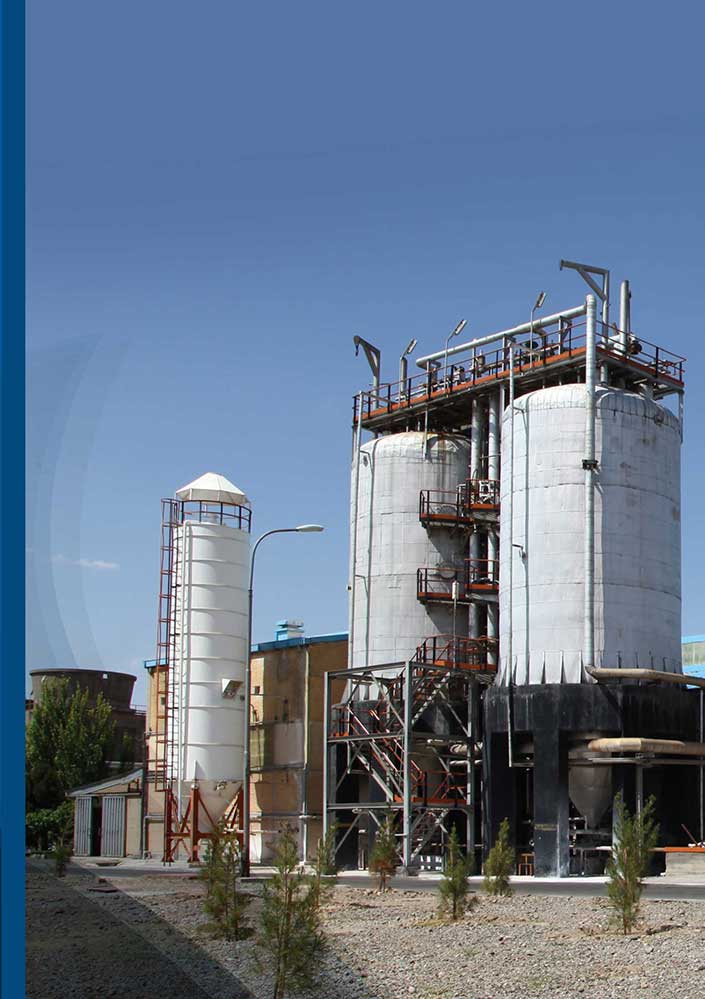
این واحد مجموعه واحدهای تولید آب صنعتی، برج خنك كننده، تولید هوای فشرده (هوای ابزار دقیق و كارگاهی) ، ازت سازی، سوخت رسانی و آب آتش نشانی ، آب آشامیدنی و آب كارگاهی و باغبانی می باشد.
- تولید آب صنعتی: دو برج فعل و انفعال با سیستم Hot Lime reaction جهت تولید آب مورد نیاز دیگهای بخار با ظرفیت اسمی 110 مترمكعب برای هر برج طراحی شده است این مجموعه شامل دو برج فعل و انفعال ، 6 عدد فیلتر زغالی و 4 عدد فیلتر رزینی جهت نرم كردن آب مورد نیاز دیگهای بخار می باشد.
- برج خنك كننده : این واحد شامل 4 دستگاه تلمبه آب چرخشی هر كدام به ظرفیت 5500 مترمكعب در ساعت و دو برج خنك كننده هركدام با هفت Cell می باشد كه عملیات خنك كردن واحدهای پالایشی توسط این مجموعه انجام می گیرد.
- تولید هوای فشرده: هوای ابزار دقیقی و صنعتی مورد نیاز بخشهای مختلف پالایشگاه در این واحد از طریق 5 دستگاه كمپرسور (یك دستگاه كمپرسور توربینی و 4 دستگاه كمپرسور برقی) تامین می شود ظرفیت تولید هوای فشرده در شرایط فعلی 18000 نرمال مترمكعب در ساعت می باشد.
- واحد تولید ازت: این واحد جهت تامین ازت مصرفی پالایشگاه برای مصارف فرآیندی و گاز پوششی مخازن ، طراحی و نصب شده است كه ظرفیت آن 450 نرمال مترمكعب در ساعت گاز ازت و 50 نرمال مترمكعب در ساعت مایع می باشد.
- سوخت رسانی: این مجموعه شامل 5 دستگاه تلمبه جهت تامین سوخت مایع مصرفی در پالایشگاه در دو بخش سوخت نفت كوره و نفتا است. سایر قسمتهای مجموعه آب صنعتی برای تامین آب آتش نشانی، آب آشامیدنی و آب كارگاهی و باغبانی طراحی شده اند.
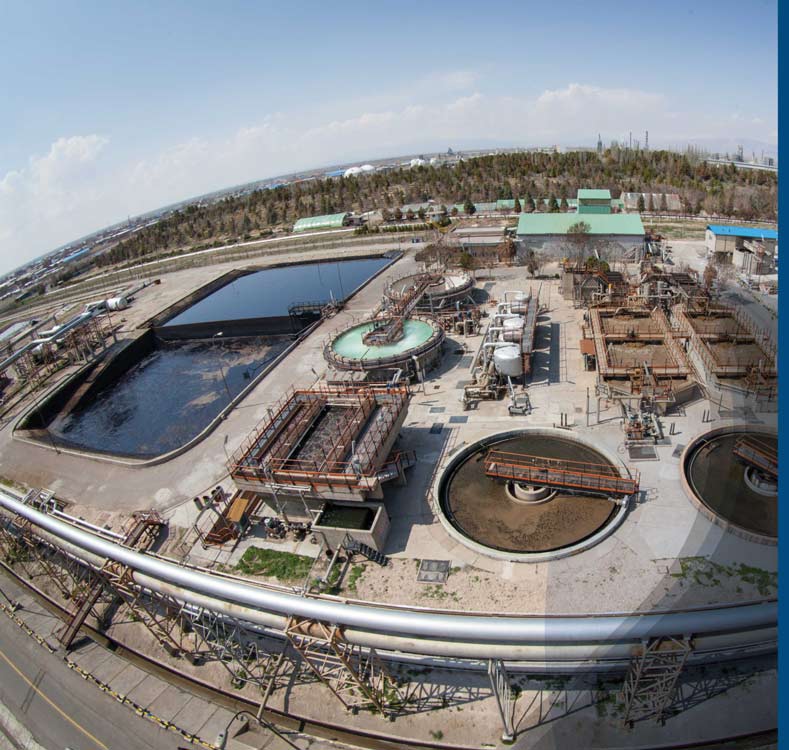
این واحد ضمن پیشگیری از توسعه آلودگی آب و خاک، مقادیر قابل ملاحظه ای آب مصرف شده را بصورت مستمر بازیافت نموده و به چرخه مصرف مجدد به برج خنك كننده برمیگرداند . بطوریکه بیش از 65 %آب جبرانی برجهای خنک کننده را تأمین می نماید. این واحد وظایف ذیل را برعهده دارد:
- تصفیه فیزیکی و بیولوژیکی آبهای آلوده به مواد آلی به میزان 160 مترمكعب در ساعت .(ظرفیت طراحی این سیستم پس از اجرای طرح دوبله سازی 240 متر مكعب در ساعت گردیده است)
- تصفیه شیمیایی آبهای آلوده به مواد شیمیایی تخلیه شده از برجهای خنك كننده، دیگهای بخار و برجهای فعل و انفعال با ظرفیت طراحی 50 مترمكعب در ساعت.
- تصفیه فاضلاب بهداشتی با ظرفیت تصفیه 10 مترمكعب در ساعت.
- تفكیك لجنهای آهكی و بیولوژیكی- نفتی: لجنهای آهكی كه حاصل از برجهای فعل و انفعال می باشد در دستگاه فیلتر پرس ، فشرده شده و به حالت نیمه خشك تبدیل می شوند كه این آهك قابل استفاده در صنایع سیمان می باشد. لجنهای نفتی و بیولوژیكی كه حاصل از عملكرد واحدهای فرآیندی و باكتریهای مورد استفاده در بخش تصفیه بیولوژیكی واحد بازیافت می باشد ، پس از هضم در حوضچه ها به دستگاه سانتریفیوژ ، ارسال و پس از آبگیری به كود قابل استفاده در توسعه فضای سبز و یا مواد غیر فعال بی ضرر جهت دفع به محیط تبدیل می گردد. ظرفیت سیستم لجن آهكی 15 مترمكعب در ساعت و سیستم بیولوژیكی 10 مترمكعب در ساعت می باشد.
این واحد ضمن پیشگیری از توسعه آلودگی آب و خاک، مقادیر قابل ملاحظه ای آب مصرف شده را بصورت مستمر بازیافت نموده و به چرخه مصرف مجدد به برج خنك كننده برمیگرداند . بطوریکه بیش از 65 %آب جبرانی برجهای خنک کننده را تأمین می نماید. این واحد وظایف ذیل را برعهده دارد:
- تصفیه فیزیکی و بیولوژیکی آبهای آلوده به مواد آلی به میزان 160 مترمكعب در ساعت .(ظرفیت طراحی این سیستم پس از اجرای طرح دوبله سازی 240 متر مكعب در ساعت گردیده است)
- تصفیه شیمیایی آبهای آلوده به مواد شیمیایی تخلیه شده از برجهای خنك كننده، دیگهای بخار و برجهای فعل و انفعال با ظرفیت طراحی 50 مترمكعب در ساعت.
- تصفیه فاضلاب بهداشتی با ظرفیت تصفیه 10 مترمكعب در ساعت.
- تفكیك لجنهای آهكی و بیولوژیكی- نفتی: لجنهای آهكی كه حاصل از برجهای فعل و انفعال می باشد در دستگاه فیلتر پرس ، فشرده شده و به حالت نیمه خشك تبدیل می شوند كه این آهك قابل استفاده در صنایع سیمان می باشد. لجنهای نفتی و بیولوژیكی كه حاصل از عملكرد واحدهای فرآیندی و باكتریهای مورد استفاده در بخش تصفیه بیولوژیكی واحد بازیافت می باشد ، پس از هضم در حوضچه ها به دستگاه سانتریفیوژ ، ارسال و پس از آبگیری به كود قابل استفاده در توسعه فضای سبز و یا مواد غیر فعال بی ضرر جهت دفع به محیط تبدیل می گردد. ظرفیت سیستم لجن آهكی 15 مترمكعب در ساعت و سیستم بیولوژیكی 10 مترمكعب در ساعت می باشد.
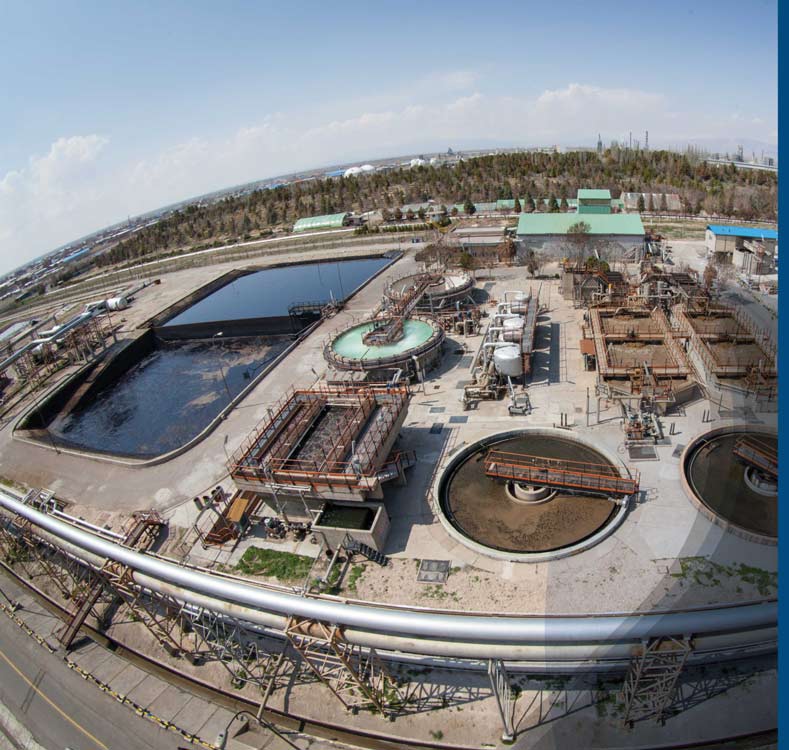
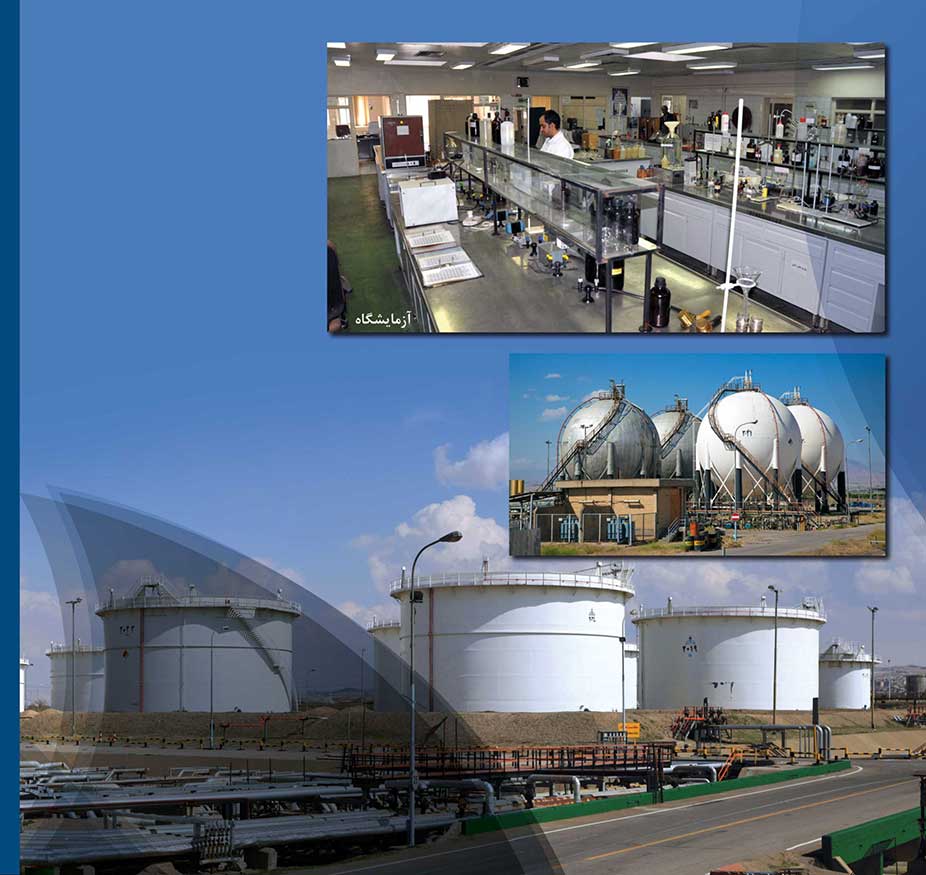
به منظور حصول اطمینان از كیفیت نفت خام و فرآورده های میانی و نهایی تولیدی پالایشگاه و ارزیابی عملكرد و كنترل واحدهای پالایشی و تولید محصولات طبق مشخصات استاندارد ، نمونه ها مطابق برنامه به آزمایشگاه شركت منتقل می شود تا در سه بخش كنترل كیفیت ، تجزیه و ویژه براساس استانداردهای بین المللی ، استاندارد ملی ایران و مشخصات تعیین شده از سوی شركت ملی پالایش و پخش فرآورده های نفتی ایران توسط دستگاههای پیشرفته روز و كارشناسان متخصص مورد آزمایش و كنترل قرار گیرد تا پس از اخذ مجوز گواهی كنترل كیفیت اجازه ورود به بازار مصرف را پیدا نمایند. آزمایشگاه شركت پالایش نفت تبریز به عنوان آزمایشگاه معتمد در منطقه ، در خصوص انجام آزمایش و ارائه گواهینامه برای نمونه های ارسالی از گمركات كشور ، موسسه تحقیقات و استاندارد صنعتی ، قوه قضائیه و مراكز علمی پژوهشی نیز فعالیت دارد.
شركت پالایش نفت تبریز برای ذخیره سازی نفت خام ، برنامه ریزی عملیات پالایشی ، ذخیره سازی خوراك واحدها ، اختلاط مواد نفتی ، اصلاح مشخصات غیر منطبق فرآورده ها و تحویل و ارسال فرآورده ها و محصولات منطبق با استاندارد شركت ملی نفت ایران ، به شركت ملی پخش و یا شركت های خصوصی ؛ 60 مخزن مواد هیدروكربنی به ظرفیت 277,772,3 بشكه را به شرح جدول ذیل در اختیار دارد:
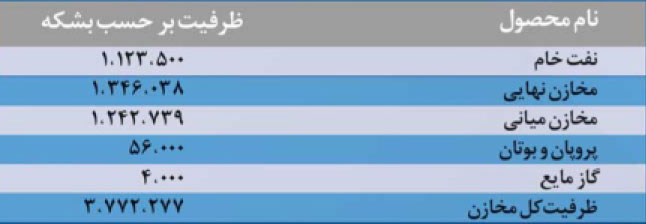
قابل توجه اینكه ، مخازن و متعلقات آن با توجه به خصوصیات فرآورده ها ، به اشكال متنوع و مختلفی طراحی و ساخته شده است از نكات قابل ذكر اینكه از مخازن كروی برای فرآورده های گازی و مخازن سقف شناور ، برای فرآورده های فرار و مخازن با گاز پوششی ، برای فرآورده هایی كه نباید با هوا تماس داشته باشد و مخازن با گرم كننده های بخار آب ، برای موادی كه زود ماسیده می شود را می توان نام برد.
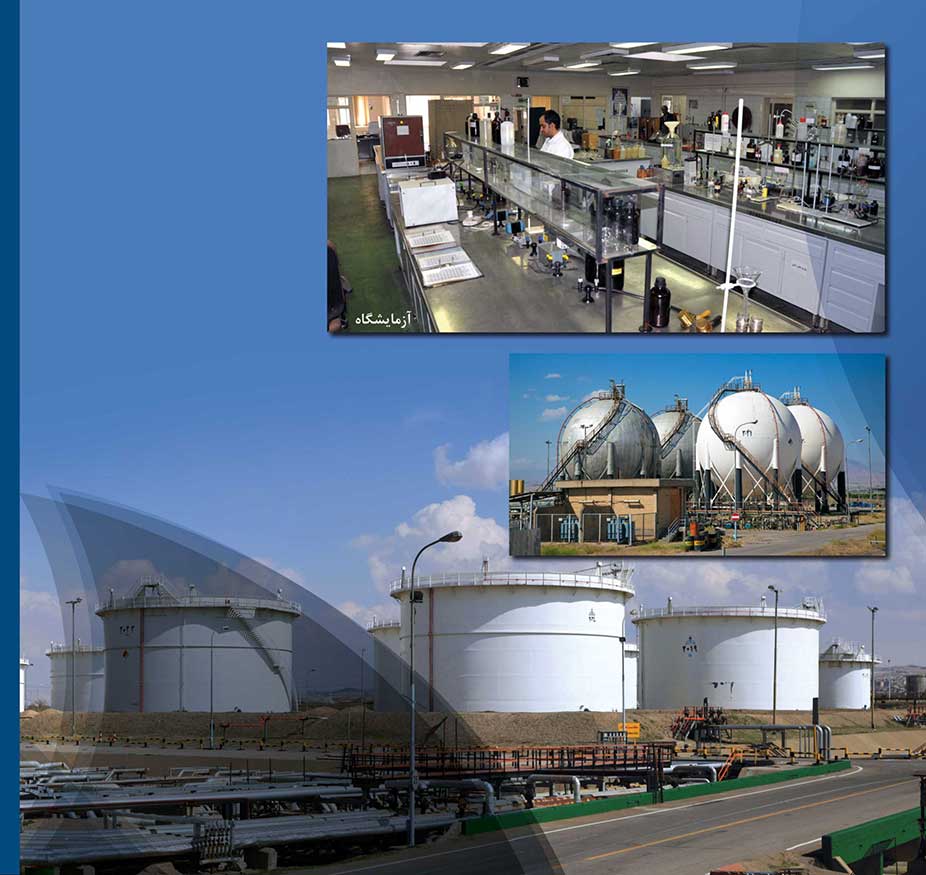
به منظور حصول اطمینان از كیفیت نفت خام و فرآورده های میانی و نهایی تولیدی پالایشگاه و ارزیابی عملكرد و كنترل واحدهای پالایشی و تولید محصولات طبق مشخصات استاندارد ، نمونه ها مطابق برنامه به آزمایشگاه شركت منتقل می شود تا در سه بخش كنترل كیفیت ، تجزیه و ویژه براساس استانداردهای بین المللی ، استاندارد ملی ایران و مشخصات تعیین شده از سوی شركت ملی پالایش و پخش فرآورده های نفتی ایران توسط دستگاههای پیشرفته روز و كارشناسان متخصص مورد آزمایش و كنترل قرار گیرد تا پس از اخذ مجوز گواهی كنترل كیفیت اجازه ورود به بازار مصرف را پیدا نمایند. آزمایشگاه شركت پالایش نفت تبریز به عنوان آزمایشگاه معتمد در منطقه ، در خصوص انجام آزمایش و ارائه گواهینامه برای نمونه های ارسالی از گمركات كشور ، موسسه تحقیقات و استاندارد صنعتی ، قوه قضائیه و مراكز علمی پژوهشی نیز فعالیت دارد.
شركت پالایش نفت تبریز برای ذخیره سازی نفت خام ، برنامه ریزی عملیات پالایشی ، ذخیره سازی خوراك واحدها ، اختلاط مواد نفتی ، اصلاح مشخصات غیر منطبق فرآورده ها و تحویل و ارسال فرآورده ها و محصولات منطبق با استاندارد شركت ملی نفت ایران ، به شركت ملی پخش و یا شركت های خصوصی ؛ 60 مخزن مواد هیدروكربنی به ظرفیت 277,772,3 بشكه را به شرح جدول ذیل در اختیار دارد:
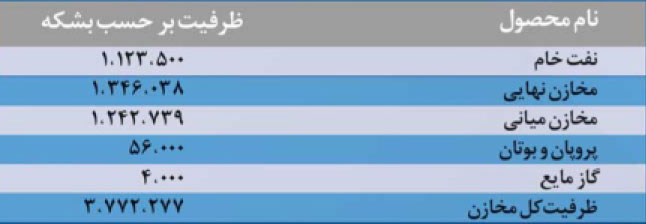
قابل توجه اینكه ، مخازن و متعلقات آن با توجه به خصوصیات فرآورده ها ، به اشكال متنوع و مختلفی طراحی و ساخته شده است از نكات قابل ذكر اینكه از مخازن كروی برای فرآورده های گازی و مخازن سقف شناور ، برای فرآورده های فرار و مخازن با گاز پوششی ، برای فرآورده هایی كه نباید با هوا تماس داشته باشد و مخازن با گرم كننده های بخار آب ، برای موادی كه زود ماسیده می شود را می توان نام برد.